So long, 2010, 2011 is upon us. Back in 1985, I could not even conceive of still being around in 2011, but here we almost are.
Sitting here trying to think up something cool to say for the New Year is coming close to leaving me fingerless (which is the same thing as ‘speechless’, if I were a radio talk show host). I know we were in the middle of talking about Industrial Planers but Christmas, and then New Years, only comes around once a year. So, here I sit.
One thing I would like to know for next year is: What do YOU need to know about? I really have no idea how many people may be reading these columns, but whoever you may be, on my best day this column is for you.
Do you have tools? Is there something wrong that you may be wondering about? Ask Me. It’s what I did for over 25 years and I’m doggone good at it.
I’m also pretty good at making people laugh, so I thought I’d close out the year with a short story: A man is flying in a hot air balloon and realizes he is lost. He reduces height and spots a man down below. He lowers the balloon further and shouts: "Excuse me, can you help me? I promised my friend I would meet him half an hour ago, but I don't know where I am." The man below says: "Yes. You are in a hot air balloon, hovering approximately 30 feet above this field. You are between 40 and 42 degrees N. latitude, and between 58 and 60 degrees W. longitude." "You must be an engineer," says the balloonist. "I am," replies the man. "How did you know?" "Well," says the balloonist, "everything you have told me is technically correct, but I have no idea what to make of your information, and the fact is I am still lost."
The man below says "You must be a manager."
"I am," replies the balloonist, "but how did you know?"
"Well," says the man, "you don't know where you are, or where you are going. You have made a promise which you have no idea how to keep, and you expect me to solve your problem. The fact is you are in the exact same position you were in before we met, but now it is somehow my fault."
Enjoy the New Years holiday weekend, may Our Lord Jesus Bless you all - send me your comments - and we’ll see you next year.
Send your questions or comments to:
Toolsmartz@bellsouth.net and we’ll see what we can do to help you.
_______________________________________________________________
Any views or opinions presented in this article are solely those of the author and do not necessarily represent those of this newspaper. Neither the author, nor this newspaper, accepts any liability for the content of this article, or for the consequences of any actions taken on the basis of the information provided.
Friday, December 31, 2010
Sunday, December 19, 2010
Column #46 - The True Reason for the Season
“Happy Holidays”…what? Uh…”Happy Holydays”? Well, that’s a little better. How about “MERRY CHRISTMAS”??? It really frosts my pumpkin to hear happy holidays. Sure some say that this time of year was a pagan holiday long before Christmas- so what? It isn’t now, and hasn’t been for hundreds of years.
Christmas 2010 is here this weekend. We hustle, we bustle and we shop until we drop. Sadly, so many of us seem to ignore the true reason for the celebration. The birth of Our Lord Jesus. My pastor has some good thoughts about the commercialization of Christmas. If I remember correctly, he says that it is really a cool deal when everyone, no matter HOW they do it, is celebrating Jesus’ birth. I must agree.
For this weekend’s column, I could find no more appropriate words than these: “Now the birth of Jesus Christ was as follows: After His mother Mary was betrothed to Joseph, before they came together, she was found with child of the Holy Spirit. Then Joseph her husband, being a just man, and not wanting to make her a public example, was minded to put her away secretly. But while he thought about these things, behold, an angel of the Lord appeared to him in a dream, saying, “Joseph, son of David, do not be afraid to take to you Mary your wife, for that which is conceived in her is of the Holy Spirit. And she will bring forth a Son, and you shall call His name JESUS, for He will save His people from their sins.” So all this was done that it might be fulfilled which was spoken by the Lord through the prophet, saying: “Behold, the virgin shall be with child, and bear a Son, and they shall call His name Immanuel,” which is translated, “God with us.” Then Joseph, being aroused from sleep, did as the angel of the Lord commanded him and took to him his wife, and did not know her till she had brought forth her firstborn Son. And he called His name JESUS.” (NKJV)
The words are there and we read them… but do they sink in? God’s Son was born… not in a palace, but in a barn. We love barns in Tennessee, but would we want our kids to be born there? Little Jesus, Son of the Most High God…in a cradle. It strains our imagination, but the written record is there. All we need do is believe.
Merry Christmas to all and May God Bless us - everyone.
Send your questions or comments to: Toolsmartz@bellsouth.net and we’ll see what we can do to help you.
_______________________________________________________________
Any views or opinions presented in this article are solely those of the author and do not necessarily represent those of this newspaper. Neither the author, nor this newspaper, accepts any liability for the content of this article, or for the consequences of any actions taken on the basis of the information provided.
Christmas 2010 is here this weekend. We hustle, we bustle and we shop until we drop. Sadly, so many of us seem to ignore the true reason for the celebration. The birth of Our Lord Jesus. My pastor has some good thoughts about the commercialization of Christmas. If I remember correctly, he says that it is really a cool deal when everyone, no matter HOW they do it, is celebrating Jesus’ birth. I must agree.
For this weekend’s column, I could find no more appropriate words than these: “Now the birth of Jesus Christ was as follows: After His mother Mary was betrothed to Joseph, before they came together, she was found with child of the Holy Spirit. Then Joseph her husband, being a just man, and not wanting to make her a public example, was minded to put her away secretly. But while he thought about these things, behold, an angel of the Lord appeared to him in a dream, saying, “Joseph, son of David, do not be afraid to take to you Mary your wife, for that which is conceived in her is of the Holy Spirit. And she will bring forth a Son, and you shall call His name JESUS, for He will save His people from their sins.” So all this was done that it might be fulfilled which was spoken by the Lord through the prophet, saying: “Behold, the virgin shall be with child, and bear a Son, and they shall call His name Immanuel,” which is translated, “God with us.” Then Joseph, being aroused from sleep, did as the angel of the Lord commanded him and took to him his wife, and did not know her till she had brought forth her firstborn Son. And he called His name JESUS.” (NKJV)
The words are there and we read them… but do they sink in? God’s Son was born… not in a palace, but in a barn. We love barns in Tennessee, but would we want our kids to be born there? Little Jesus, Son of the Most High God…in a cradle. It strains our imagination, but the written record is there. All we need do is believe.
Merry Christmas to all and May God Bless us - everyone.
Send your questions or comments to: Toolsmartz@bellsouth.net and we’ll see what we can do to help you.
_______________________________________________________________
Any views or opinions presented in this article are solely those of the author and do not necessarily represent those of this newspaper. Neither the author, nor this newspaper, accepts any liability for the content of this article, or for the consequences of any actions taken on the basis of the information provided.
Sunday, December 12, 2010
Column #45 - The continuing saga of snipe
As I had said a week or two ago, I am still a rookie at the newspaper column business and it reared its head in my column from last week.
There was a very important paragraph that got mangled up because I used odd characters. Here is what came out… “In other words, if you need a _” thick piece, take your adjustment to 1” and bring it down to _. Do not start at _” and go up to _ and then plane it. If you do that, you are leaving the backlash in the lead screws & nuts and that will be increasing your chance of snipe.”
As you can see, the dimensions I was referencing got obliterated. I thought I had best rewrite the paragraph so that my meaning is crystal clear. Here is what I meant to say. ”In other words, if you need a Three-Quarter-Inch thick piece, take your adjustment to One-Inch and bring it down to Three-Quarter-Inch. Do not start at One-Half-Inch and go up to Three-Quarter-Inch and then plane it. If you do that, you are leaving the backlash in the lead screws & nuts and that will be increasing your chance of snipe.” Hopefully, you can see the difference and why it is important.
Alright on to new business - the Industrial Planer. Most Industrial Planers have bed rollers and they are height-adjustable. Ideally, bed rollers are for use when you are planning very rough or warped boards. Yes, planning warped boards is not a good idea; however, in certain instances (like sawmills) one needs to make a pass through a planer and then go on to other machines. In most IP’s, the bed rollers are directly underneath the infeed rollers. This helps put the ‘squeeze’ on the stock as its going through the planer. As I said, the bed rollers are usually height-adjustable and very rough boards can use a bed roller height at 5 to 10 thousandths. If one is trying to get a snipe-free surface, the height of the bed rollers should be level with the bed or even 1 to 2 thousandths below the bed. If a smooth surface is the objective, having the bed rollers above the surface of the bed can actually create snipe because of the upward force of the board as it bumps up onto the bed roller.
Yes, there are many issues with an Industrial Planer, and it’s gonna take quite a few columns to work through them. I’ve got time, do you?
See ya next weekl
Send your questions or comments to:
Toolsmartz@bellsouth.net and we’ll see what we can do to help you.
_______________________________________________________________
Any views or opinions presented in this article are solely those of the author and do not necessarily represent those of this newspaper. Neither the author, nor this newspaper, accepts any liability for the content of this article, or for the consequences of any actions taken on the basis of the information provided.
There was a very important paragraph that got mangled up because I used odd characters. Here is what came out… “In other words, if you need a _” thick piece, take your adjustment to 1” and bring it down to _. Do not start at _” and go up to _ and then plane it. If you do that, you are leaving the backlash in the lead screws & nuts and that will be increasing your chance of snipe.”
As you can see, the dimensions I was referencing got obliterated. I thought I had best rewrite the paragraph so that my meaning is crystal clear. Here is what I meant to say. ”In other words, if you need a Three-Quarter-Inch thick piece, take your adjustment to One-Inch and bring it down to Three-Quarter-Inch. Do not start at One-Half-Inch and go up to Three-Quarter-Inch and then plane it. If you do that, you are leaving the backlash in the lead screws & nuts and that will be increasing your chance of snipe.” Hopefully, you can see the difference and why it is important.
Alright on to new business - the Industrial Planer. Most Industrial Planers have bed rollers and they are height-adjustable. Ideally, bed rollers are for use when you are planning very rough or warped boards. Yes, planning warped boards is not a good idea; however, in certain instances (like sawmills) one needs to make a pass through a planer and then go on to other machines. In most IP’s, the bed rollers are directly underneath the infeed rollers. This helps put the ‘squeeze’ on the stock as its going through the planer. As I said, the bed rollers are usually height-adjustable and very rough boards can use a bed roller height at 5 to 10 thousandths. If one is trying to get a snipe-free surface, the height of the bed rollers should be level with the bed or even 1 to 2 thousandths below the bed. If a smooth surface is the objective, having the bed rollers above the surface of the bed can actually create snipe because of the upward force of the board as it bumps up onto the bed roller.
Yes, there are many issues with an Industrial Planer, and it’s gonna take quite a few columns to work through them. I’ve got time, do you?
See ya next weekl
Send your questions or comments to:
Toolsmartz@bellsouth.net and we’ll see what we can do to help you.
_______________________________________________________________
Any views or opinions presented in this article are solely those of the author and do not necessarily represent those of this newspaper. Neither the author, nor this newspaper, accepts any liability for the content of this article, or for the consequences of any actions taken on the basis of the information provided.
Column #44 - Our ‘snipe hunt’ continues.
Last week, I gave you the most basic description of what snipe is and how it happens. The “why” it happens and how to minimize it, is the subject of this week’s column.
Setting the stage, your lunchbox planer has a movable head for depth of cut. It has no bed rollers, and the distance between the infeed roller and the outfeed roller is 4 inches. With that foundation, our snipe would be 2” long at the front and 2” long at the rear of the board. “Why” do you ask? Good question.
Here’s why- as long as the board is underneath both rollers, the head will be shoved upward by the force of the rollers pushing down against the board.
The early lunchbox planer designs were notorious for the problem of snipe. Later designs, and the ones most often found now, had a head locking mechanism made into the planer that allowed the operator to actually lock the head in place, which has pretty much eliminated snipeing on this design.
One thing that will do much to decrease your snipeing is [on the movable head style] to ALWAYS make your final depth of cut setting by moving the head downward. If you will do this, it will remove the backlash out of the lead screws [the threaded rods that the planer head moves up and down on] and their nuts. In other words, if you need a ¾” thick piece, take your adjustment to 1” and bring it down to ¾. Do not start at ½” and go up to ¾ and then plane it. If you do that, you are leaving the backlash in the lead screws & nuts and that will be increasing your chance of snipe.
On the early design lunchboxes, there were many different methods attempted to eliminate snipe. Some were easy, some were weird and most did not work every time. Once the planer makers figured out that customers were not in the mood to accept snipe as a way of life, they went back to the drawing board and did something about it. Hence, the head lock I mentioned earlier.
So far, we’ve been talking only about the lunchbox planers. Let me tell you straight up, snipe on industrial planers is a real happening, too. The Industrial planers have an inherent advantage because most of them have a movable bed, not head. This design difference makes snipe a lot easier to control, but there are so many adjustments that other things can go wrong. We’ll ‘go there’ next time.
Send your questions or comments to:
Toolsmartz@bellsouth.net and we’ll see what we can do to help you.
_______________________________________________________________
Any views or opinions presented in this article are solely those of the author and do not necessarily represent those of this newspaper. Neither the author, nor this newspaper, accepts any liability for the content of this article, or for the consequences of any actions taken on the basis of the information provided.
Setting the stage, your lunchbox planer has a movable head for depth of cut. It has no bed rollers, and the distance between the infeed roller and the outfeed roller is 4 inches. With that foundation, our snipe would be 2” long at the front and 2” long at the rear of the board. “Why” do you ask? Good question.
Here’s why- as long as the board is underneath both rollers, the head will be shoved upward by the force of the rollers pushing down against the board.
The early lunchbox planer designs were notorious for the problem of snipe. Later designs, and the ones most often found now, had a head locking mechanism made into the planer that allowed the operator to actually lock the head in place, which has pretty much eliminated snipeing on this design.
One thing that will do much to decrease your snipeing is [on the movable head style] to ALWAYS make your final depth of cut setting by moving the head downward. If you will do this, it will remove the backlash out of the lead screws [the threaded rods that the planer head moves up and down on] and their nuts. In other words, if you need a ¾” thick piece, take your adjustment to 1” and bring it down to ¾. Do not start at ½” and go up to ¾ and then plane it. If you do that, you are leaving the backlash in the lead screws & nuts and that will be increasing your chance of snipe.
On the early design lunchboxes, there were many different methods attempted to eliminate snipe. Some were easy, some were weird and most did not work every time. Once the planer makers figured out that customers were not in the mood to accept snipe as a way of life, they went back to the drawing board and did something about it. Hence, the head lock I mentioned earlier.
So far, we’ve been talking only about the lunchbox planers. Let me tell you straight up, snipe on industrial planers is a real happening, too. The Industrial planers have an inherent advantage because most of them have a movable bed, not head. This design difference makes snipe a lot easier to control, but there are so many adjustments that other things can go wrong. We’ll ‘go there’ next time.
Send your questions or comments to:
Toolsmartz@bellsouth.net and we’ll see what we can do to help you.
_______________________________________________________________
Any views or opinions presented in this article are solely those of the author and do not necessarily represent those of this newspaper. Neither the author, nor this newspaper, accepts any liability for the content of this article, or for the consequences of any actions taken on the basis of the information provided.
Sunday, December 5, 2010
Column #43 - Yes, a ‘snipe hunt’ is a real thing.
It’s Thanksgiving weekend as I write this and since I am new to the art of writing a weekly column- well, yea, I’ve done a few, but this is my first Holiday season- I am just learning that I should be a week ahead if I want my column to seem ‘on time’. Point being, I should have used last week’s column to wish everyone Happy Thanksgiving! Now, by the time you read this, T-day will have been gone for a week. Anyway, I’ll get better and more timely as I learn.
This week I’d like to introduce you to one of the most frequent problems of a planer. Snipe. Yes, it really IS called that…among other things. The basic symptom is that after the board has been run through the planer, the thickness of the ends is thinner than the middle of the board. Remembering that the purpose of a planer is to make the board the same thickness in all areas, Snipe is not an acceptable outcome.
Snipe can also be known as ‘cut out’; ‘dip out’; ‘notching’- names like that.
Essentially tho, one looks at the board surface and sees where, for the first few inches and usually the last few inches, the knives have made a deeper cut than they do on the rest of the board. For the purpose of our discussion, we’re going to limit ourselves to lunchbox planers that do not have bed rollers. [Bed rollers, which are mostly found on industrial planers. create other situations that we aren’t ready to talk about].
Alright, so you’ve sent a board thru and you see and feel snipe on the ends of the board. The first thing to realize is that this is being caused by the head of the planer rising as the board gets underneath both feed rollers. Again, we’re talking about lunchbox planers that usually are pretty simple- they have a fixed bed and a movable head. The head moves up and down to adjust the thickness of the cut.
So what happens- as the board is placed on the bed and pushed into the planer, the infeed roller grabs it and pulls it in, about 2 inches into the planer, the board runs underneath the knives and starts being cut. About 2 inches after that, the board runs underneath the outfeed roller and starts being pulled by both rollers, AND this is where the snipe stops… on the front end of the board. As it comes out, it leaves the infeed roller and snipe starts on the trailing end of the board. In this case you would have a 2” snipe on each end of the board.
Lots of background I know, but knowing the basics is essential to knowing why snipe occurs and what to do about it.
Send your questions or comments to:
Toolsmartz@bellsouth.net and we’ll see what we can do to help you.
_______________________________________________________________
Any views or opinions presented in this article are solely those of the author and do not necessarily represent those of this newspaper. Neither the author, nor this newspaper, accepts any liability for the content of this article, or for the consequences of any actions taken on the basis of the information provided
This week I’d like to introduce you to one of the most frequent problems of a planer. Snipe. Yes, it really IS called that…among other things. The basic symptom is that after the board has been run through the planer, the thickness of the ends is thinner than the middle of the board. Remembering that the purpose of a planer is to make the board the same thickness in all areas, Snipe is not an acceptable outcome.
Snipe can also be known as ‘cut out’; ‘dip out’; ‘notching’- names like that.
Essentially tho, one looks at the board surface and sees where, for the first few inches and usually the last few inches, the knives have made a deeper cut than they do on the rest of the board. For the purpose of our discussion, we’re going to limit ourselves to lunchbox planers that do not have bed rollers. [Bed rollers, which are mostly found on industrial planers. create other situations that we aren’t ready to talk about].
Alright, so you’ve sent a board thru and you see and feel snipe on the ends of the board. The first thing to realize is that this is being caused by the head of the planer rising as the board gets underneath both feed rollers. Again, we’re talking about lunchbox planers that usually are pretty simple- they have a fixed bed and a movable head. The head moves up and down to adjust the thickness of the cut.
So what happens- as the board is placed on the bed and pushed into the planer, the infeed roller grabs it and pulls it in, about 2 inches into the planer, the board runs underneath the knives and starts being cut. About 2 inches after that, the board runs underneath the outfeed roller and starts being pulled by both rollers, AND this is where the snipe stops… on the front end of the board. As it comes out, it leaves the infeed roller and snipe starts on the trailing end of the board. In this case you would have a 2” snipe on each end of the board.
Lots of background I know, but knowing the basics is essential to knowing why snipe occurs and what to do about it.
Send your questions or comments to:
Toolsmartz@bellsouth.net and we’ll see what we can do to help you.
_______________________________________________________________
Any views or opinions presented in this article are solely those of the author and do not necessarily represent those of this newspaper. Neither the author, nor this newspaper, accepts any liability for the content of this article, or for the consequences of any actions taken on the basis of the information provided
Friday, November 19, 2010
Column #42 - Is it Dull Knives, or something else?
I just got to thinking that these past couple of columns have been more and more like a Saturday morning cliff-hanger…I set out the problem and just when you think I’m gonna give up the answer, I put it off until next week…?
Alright, this week, I really will give you the final solution to the problem.
We do need to recap, if we have some new readers…So here it is: you’ve been using your lunchbox planer, and it has been working just fine…but all of a sudden, it refuses to plane the wood. You can’t even shove the wood in and get it to work. It used to be that it practically pulled the wood out of your hand as you fed it…now, it ain’t happening. Last week, we brought up a dirty, or pitch encrusted bed surface and dirty or wood flour-caked-up feed rollers.
I left you with a teaser about there being one more solution that many people think should be number 1 on the list.
Here it is… Dull knives. Yep, that’s it. I have seen many a planer, just quit planning and the owner changes the knives, or flips his over to a fresh edge, and the planer resumes ‘doing it’s thing’ just fine. One needs to understand that when the knives get dull, they start beating on the wood and they actually create more resistance to the job the feed rollers can do (that being push the wood through the planer). Yes, changing the knives CAN do that.
Now, if you’ve read the past couple of columns, you may be asking: “If it’s that simple, why didn’t he just say so?” Well, here’s why… let’s pretend that your planer quit working as we have described and you change the knives…and…it…still…doesn’t…feed. Now what? Well. More than likely, your problem was a dirty bed or caked up feed rollers (or maybe both)…which you will now have to clean, with those freshly sharpened knives right within a finger’s reach. Do you know how easily fresh knives will cut flesh? LIKE BUTTER.
So, as I suggested, clean the bed and the rollers first. That way, your fingers are at least close to used knives. Don’t get me wrong, they will still cut the mess out of you, but not quite as easy as fresh knives will.
Also, there is a possibility that you will get more board feet cut with your knives before you need to change them, if you will clean the bed and rollers first. That was my thinking behind my suggestions.
Send your questions or comments to:
Toolsmartz@bellsouth.net and we’ll see what we can do to help you.
_______________________________________________________________
Any views or opinions presented in this article are solely those of the author and do not necessarily represent those of this newspaper. Neither the author, nor this newspaper, accepts any liability for the content of this article, or for the consequences of any actions taken on the basis of the information provided.
Alright, this week, I really will give you the final solution to the problem.
We do need to recap, if we have some new readers…So here it is: you’ve been using your lunchbox planer, and it has been working just fine…but all of a sudden, it refuses to plane the wood. You can’t even shove the wood in and get it to work. It used to be that it practically pulled the wood out of your hand as you fed it…now, it ain’t happening. Last week, we brought up a dirty, or pitch encrusted bed surface and dirty or wood flour-caked-up feed rollers.
I left you with a teaser about there being one more solution that many people think should be number 1 on the list.
Here it is… Dull knives. Yep, that’s it. I have seen many a planer, just quit planning and the owner changes the knives, or flips his over to a fresh edge, and the planer resumes ‘doing it’s thing’ just fine. One needs to understand that when the knives get dull, they start beating on the wood and they actually create more resistance to the job the feed rollers can do (that being push the wood through the planer). Yes, changing the knives CAN do that.
Now, if you’ve read the past couple of columns, you may be asking: “If it’s that simple, why didn’t he just say so?” Well, here’s why… let’s pretend that your planer quit working as we have described and you change the knives…and…it…still…doesn’t…feed. Now what? Well. More than likely, your problem was a dirty bed or caked up feed rollers (or maybe both)…which you will now have to clean, with those freshly sharpened knives right within a finger’s reach. Do you know how easily fresh knives will cut flesh? LIKE BUTTER.
So, as I suggested, clean the bed and the rollers first. That way, your fingers are at least close to used knives. Don’t get me wrong, they will still cut the mess out of you, but not quite as easy as fresh knives will.
Also, there is a possibility that you will get more board feet cut with your knives before you need to change them, if you will clean the bed and rollers first. That was my thinking behind my suggestions.
Send your questions or comments to:
Toolsmartz@bellsouth.net and we’ll see what we can do to help you.
_______________________________________________________________
Any views or opinions presented in this article are solely those of the author and do not necessarily represent those of this newspaper. Neither the author, nor this newspaper, accepts any liability for the content of this article, or for the consequences of any actions taken on the basis of the information provided.
Thursday, November 4, 2010
Column #39 - The ‘Hidden Art’ of the Wood Planer
This week is the lead off column of a series on a machine that many woodworkers find to have an almost ‘mystical’ air about it. This is the Wood Planer or, as it is known in Europe, the wood thicknesser. In all fairness, “thicknesser” is a more appropriate description of what the machine actually does, than is the name ‘planer’. While handtool history is not my ‘thing’, I suspect that the thicknessers acquired the name ‘planer’ simply because what they did was so similar to a hand plane that smoothes a boards surface.
Over my many years in the industry, I don’t suppose there was ever another machine that caused as many headaches and problems for my customers as did the planer. I think most of that was because the average woodworker just doesn’t understand how these things work, and because the typical planer has so many adjustments that it is a bit intimidating.
The best starting place for our discussions is most likely to define the types of planers that are out there. Decent sized shops would have a planer that would be capable of planing 18” – 20” – 24” or even 36” wide stock. These types of planers are the ones with all those adjustments I mentioned because they have chipbreakers, pressure bars, spring-loaded infeed and outfeed rollers and bed rollers. All of those components must be adjusted properly and they have to be adjusted with consideration given to each of the other components. This is what I call an Industrial Planer.
Further down the scale is the planer that is typically found in home workshops. It’s easily portable and usually has a capacity of only 12”- 15” wide. These planers do not have pressure bars or chipbreakers or bed rollers. As you can see, the number of adjustments is way down from the Industrial types. These planers are fondly called “lunchbox” planers.
I think we will start or series off talking about lunchbox planers because I think that is the most likely type of planer my readers would have. Now, I could be wrong and if I am, I trust those of you who may have industrial planers in your shop to drop me a note and let me know.
Most lunchbox planers are ready to use, right out of the box. Oh, there might be some accessory tables to add or a stand to put together, but essentially the planer is ready to plane wood… and that is a bonus for the buyer.
Let’s pause here for the week. See ya next time…
Send your questions or comments to:
Toolsmartz@bellsouth.net and we’ll see what we can do to help you.
Over my many years in the industry, I don’t suppose there was ever another machine that caused as many headaches and problems for my customers as did the planer. I think most of that was because the average woodworker just doesn’t understand how these things work, and because the typical planer has so many adjustments that it is a bit intimidating.
The best starting place for our discussions is most likely to define the types of planers that are out there. Decent sized shops would have a planer that would be capable of planing 18” – 20” – 24” or even 36” wide stock. These types of planers are the ones with all those adjustments I mentioned because they have chipbreakers, pressure bars, spring-loaded infeed and outfeed rollers and bed rollers. All of those components must be adjusted properly and they have to be adjusted with consideration given to each of the other components. This is what I call an Industrial Planer.
Further down the scale is the planer that is typically found in home workshops. It’s easily portable and usually has a capacity of only 12”- 15” wide. These planers do not have pressure bars or chipbreakers or bed rollers. As you can see, the number of adjustments is way down from the Industrial types. These planers are fondly called “lunchbox” planers.
I think we will start or series off talking about lunchbox planers because I think that is the most likely type of planer my readers would have. Now, I could be wrong and if I am, I trust those of you who may have industrial planers in your shop to drop me a note and let me know.
Most lunchbox planers are ready to use, right out of the box. Oh, there might be some accessory tables to add or a stand to put together, but essentially the planer is ready to plane wood… and that is a bonus for the buyer.
Let’s pause here for the week. See ya next time…
Send your questions or comments to:
Toolsmartz@bellsouth.net and we’ll see what we can do to help you.
Column #38 - The Adventure of the 1955 Nomad
Well, let’s see, after 5 hard weeks of ‘machine talkin’ it’s about time for another of my famous ‘detours’. This one is into the world of car shows and the adventures that come with ‘em.
Back on October 16th, I took Mrs. Mayberry over to Cool Springs for the Battleground AACA Region’s annual show. They wound up having a record turnout of almost 300 cars. The 1966 Batmobile was even there - how kool is that? I had an ulterior motive for going because of a couple of reasons. First, I needed to hand out some flyers about our cruise-in at Cannonsburgh and second, back last summer our club renovated our clubhouse and we found a poster from Battleground’s 2nd car show. It was in great shape for a poster that had been hanging on our bathroom wall for over 20 years. Anyway, I thought that club would be glad to see one of their old posters returned to them, so I took it over. They were thrilled to see it, much less actually have it given to them. I think we spread some real good will on that one.
As it sometimes the case, this show did not go down without an “adventure”.
An “adventure” is what I call it when things do not go as I plan – and you can read that as “things get really messed UP!”.
During the day I had noticed this really pretty 1955 Chevrolet Nomad wagon sitting in front of Sears and the owner was elbows deep under the hood. I had stopped by early in the day to check in and he seemed to have enough tools to do whatever needed doing, so I wished him well and went about the day. Well, sure enough, the show ended and during the wrap up, I noticed the Nomad again - still sitting where it had been all day long…and the guy’s feet were hanging out from under the dash. This cannot be good.
It wasn’t. As it turned out, the poor fellow had lost power in his electrical system and he was trying to find it again. I just happened to have a multi-meter in my tool box, so he borrowed it and started checking for voltage. We even had a fellow stop who owns a restoration shop and we all had at it. We found where the problem should have been and thought that we could jumper around that area and at least get him home. We actually got the car cranked for the first time in about 7 hours. Only…yea, I know…inside an “adventure” there is pretty much always an “only”…the underdash wiring started getting hot, caught on fire, burned a spot on his dash and we sprayed fire extinguisher dust all under the dash… what a mess…but we did NOT let his car burn down. At last report, they called AAA and got the car back to McMinnville where it remains bedded down in its nest. The Nomad’s owner and his wife seem to be real nice folks, who I would not have minded meeting on any day…I just hate that it was because of his car problem.
Send your questions or comments to:
Toolsmartz@bellsouth.net and we’ll see what we can do to help you.
Back on October 16th, I took Mrs. Mayberry over to Cool Springs for the Battleground AACA Region’s annual show. They wound up having a record turnout of almost 300 cars. The 1966 Batmobile was even there - how kool is that? I had an ulterior motive for going because of a couple of reasons. First, I needed to hand out some flyers about our cruise-in at Cannonsburgh and second, back last summer our club renovated our clubhouse and we found a poster from Battleground’s 2nd car show. It was in great shape for a poster that had been hanging on our bathroom wall for over 20 years. Anyway, I thought that club would be glad to see one of their old posters returned to them, so I took it over. They were thrilled to see it, much less actually have it given to them. I think we spread some real good will on that one.
As it sometimes the case, this show did not go down without an “adventure”.
An “adventure” is what I call it when things do not go as I plan – and you can read that as “things get really messed UP!”.
During the day I had noticed this really pretty 1955 Chevrolet Nomad wagon sitting in front of Sears and the owner was elbows deep under the hood. I had stopped by early in the day to check in and he seemed to have enough tools to do whatever needed doing, so I wished him well and went about the day. Well, sure enough, the show ended and during the wrap up, I noticed the Nomad again - still sitting where it had been all day long…and the guy’s feet were hanging out from under the dash. This cannot be good.
It wasn’t. As it turned out, the poor fellow had lost power in his electrical system and he was trying to find it again. I just happened to have a multi-meter in my tool box, so he borrowed it and started checking for voltage. We even had a fellow stop who owns a restoration shop and we all had at it. We found where the problem should have been and thought that we could jumper around that area and at least get him home. We actually got the car cranked for the first time in about 7 hours. Only…yea, I know…inside an “adventure” there is pretty much always an “only”…the underdash wiring started getting hot, caught on fire, burned a spot on his dash and we sprayed fire extinguisher dust all under the dash… what a mess…but we did NOT let his car burn down. At last report, they called AAA and got the car back to McMinnville where it remains bedded down in its nest. The Nomad’s owner and his wife seem to be real nice folks, who I would not have minded meeting on any day…I just hate that it was because of his car problem.
Send your questions or comments to:
Toolsmartz@bellsouth.net and we’ll see what we can do to help you.
Column #37 - Keeping iron dust off your floor
Once upon a time, when your columnist started this effort, he was told that no subject was unapproachable. We may be fixing to find out if that is true or not, because this column is a thinly disguised want ad. You will learn something you may not have known, but you will also get a sales pitch.
Ferrous metal dust (dust with iron in it) is obviously a problem in those shops where a lot of grinding is done, and I suspect that more than one local shop has had some issues with OSHA because of it. Way back when I was with Delta, we sold a fantastic ferrous metal dust collector. The unit was made by Torit and they are among the best at what they do. As it turned out, I became the owner of a brand new 3/4HP single phase unit. It was either take it home, or watch it go in the dumpster. So, being the tool hoarder that I am… anyway, it is a great machine that I have never run. It would be great hooked to an industrial pedestal grinder, it has two suction inlets.
This type of dust collector is strictly made for ferrous metal. One would not want to use it on aluminum or wood, and heaven forbid, aluminum AND wood. Here’s the learning part I mentioned: If you collect aluminum and wood dust in the same container, you have the basic compound of gunpowder…and all it would take is a spark of hot metal tossed into it, to produce an explosion or at least a decent fire. NEVER do this.
So, to prevent this type of event, Torit made (and Delta sold) these dust collectors strictly for ferrous metal use. It is capable of moving 500 CFM and develops a static suction of 3.5 inches of water. It has a set of filter bags in the bottom of the cabinet and the dust is shaken out of them by means of a foot pedal.
Alright - bottom line - I have this thing and I need to sell it. The last list prices of what I have were: the unit itself= $2044.00 ; a new extra set of filter bags= $875.00 ; an accessory air filtration unit= $250.00. As I said, I have never even fired it up. These prices were current in 1993. Heavens knows what they would cost today.
If you’d like to research this a bit more, the Delta model Number was 49-826- I don’t think they sell these any more. If you’re interested in this- send me an email and let’s talk, I’m very easy to negotiate with.
‘Til next week.
Send your questions or comments to:
Toolsmartz@bellsouth.net and we’ll see what we can do to help you.
_______________________________________________________________
Ferrous metal dust (dust with iron in it) is obviously a problem in those shops where a lot of grinding is done, and I suspect that more than one local shop has had some issues with OSHA because of it. Way back when I was with Delta, we sold a fantastic ferrous metal dust collector. The unit was made by Torit and they are among the best at what they do. As it turned out, I became the owner of a brand new 3/4HP single phase unit. It was either take it home, or watch it go in the dumpster. So, being the tool hoarder that I am… anyway, it is a great machine that I have never run. It would be great hooked to an industrial pedestal grinder, it has two suction inlets.
This type of dust collector is strictly made for ferrous metal. One would not want to use it on aluminum or wood, and heaven forbid, aluminum AND wood. Here’s the learning part I mentioned: If you collect aluminum and wood dust in the same container, you have the basic compound of gunpowder…and all it would take is a spark of hot metal tossed into it, to produce an explosion or at least a decent fire. NEVER do this.
So, to prevent this type of event, Torit made (and Delta sold) these dust collectors strictly for ferrous metal use. It is capable of moving 500 CFM and develops a static suction of 3.5 inches of water. It has a set of filter bags in the bottom of the cabinet and the dust is shaken out of them by means of a foot pedal.
Alright - bottom line - I have this thing and I need to sell it. The last list prices of what I have were: the unit itself= $2044.00 ; a new extra set of filter bags= $875.00 ; an accessory air filtration unit= $250.00. As I said, I have never even fired it up. These prices were current in 1993. Heavens knows what they would cost today.
If you’d like to research this a bit more, the Delta model Number was 49-826- I don’t think they sell these any more. If you’re interested in this- send me an email and let’s talk, I’m very easy to negotiate with.
‘Til next week.
Send your questions or comments to:
Toolsmartz@bellsouth.net and we’ll see what we can do to help you.
_______________________________________________________________
Sunday, September 26, 2010
#36- RAS-styles & alignment
Radial Arm Saws (RAS) are best known for being used to perform repetitive cutoffs on wider, or longer, boards. I have seen extension tables that would allow someone to lay up 30-foot boards and cut them shorter. This would be very hard to do on a table saw. A RAS can do that very easy because the head moves, not the actual workpiece.
Speaking of the head moving, there are two types of RAS’s. The first and most economical is the “regular style”. I call it that because I don’t believe there is an actual name for it. This RAS simply has an upright column at the rear and that has an arm attached to it that is sticking out from it towards the user. That arm has a grooved track built into it and the head’s roller bearings ride along those grooves to allow it to slide fore & aft. This saw is the one most seen in home shops and it is very fussy about aligning properly. At the outer end of the track, arm flex can be an issue.
The more professional design is the “turret-arm” RAS. The rear column is still there, as is the arm coming towards the user…but that arm is only ½ as long and it has a pivot point for the actual arm that has the track in it. The track arm- picture an upside down T, with the track being in the crossbar of the T and the stem being the pivot point- contains the grooves for the head’s roller bearings. This type RAS is far easier to align and has much less flex than the ‘regular’ design.
With a turret-arm RAS, achieving proper saw alignment is easier because having the track pivot in the middle allows the adjustment to better control the track arm. With the regular style, when the head is at the end closest to the user, there is always some flex. Maybe not much, but some…and the user has to factor that in when making their cuts.
Aligning a RAS is not all that complicated. I always suggest that the user get a piece of stock that is as wide as their saw can handle, lay it on the table, make a cutoff pass and check it with a framing square. Note: I don’t like using framing squares under normal conditions, but it’s about the only thing that has the capacity to check a wide-cutting RAS. Once the cutoff is checked, then the adjustments can be made. On a regular RAS, the alignment screws are located at the rear junction of the track arm and the column. On a turret-arm, the adjustment is made at the centered pivot point.
Follow your owner’s manual, check your adjustment results by making another cut off of the wide board and you’ll have your saw cutting straight in no time.
Send your questions or comments to:
Toolsmartz@bellsouth.net and we’ll see what we can do to help you.
_______________________________________________________________
Any views or opinions presented in this article are solely those of the author and do not necessarily represent those of this newspaper. Neither the author, nor this newspaper, accepts any liability for the content of this article, or for the consequences of any actions taken on the basis of the information provided.
Speaking of the head moving, there are two types of RAS’s. The first and most economical is the “regular style”. I call it that because I don’t believe there is an actual name for it. This RAS simply has an upright column at the rear and that has an arm attached to it that is sticking out from it towards the user. That arm has a grooved track built into it and the head’s roller bearings ride along those grooves to allow it to slide fore & aft. This saw is the one most seen in home shops and it is very fussy about aligning properly. At the outer end of the track, arm flex can be an issue.
The more professional design is the “turret-arm” RAS. The rear column is still there, as is the arm coming towards the user…but that arm is only ½ as long and it has a pivot point for the actual arm that has the track in it. The track arm- picture an upside down T, with the track being in the crossbar of the T and the stem being the pivot point- contains the grooves for the head’s roller bearings. This type RAS is far easier to align and has much less flex than the ‘regular’ design.
With a turret-arm RAS, achieving proper saw alignment is easier because having the track pivot in the middle allows the adjustment to better control the track arm. With the regular style, when the head is at the end closest to the user, there is always some flex. Maybe not much, but some…and the user has to factor that in when making their cuts.
Aligning a RAS is not all that complicated. I always suggest that the user get a piece of stock that is as wide as their saw can handle, lay it on the table, make a cutoff pass and check it with a framing square. Note: I don’t like using framing squares under normal conditions, but it’s about the only thing that has the capacity to check a wide-cutting RAS. Once the cutoff is checked, then the adjustments can be made. On a regular RAS, the alignment screws are located at the rear junction of the track arm and the column. On a turret-arm, the adjustment is made at the centered pivot point.
Follow your owner’s manual, check your adjustment results by making another cut off of the wide board and you’ll have your saw cutting straight in no time.
Send your questions or comments to:
Toolsmartz@bellsouth.net and we’ll see what we can do to help you.
_______________________________________________________________
Any views or opinions presented in this article are solely those of the author and do not necessarily represent those of this newspaper. Neither the author, nor this newspaper, accepts any liability for the content of this article, or for the consequences of any actions taken on the basis of the information provided.
#35 - RAS- choose the best blade
More of our on-going discussion about the Radial Arm Saw… Let’s see, where were we?... oh yes, we ended up talking about Positive and Negative blade hook angles.
My best description of how to check a sawblade’s hook angle was the ‘intersecting line method’ that I outlined last week. My second-most used visual to help understand this is that of a swimmer’s hand. If the hand is scooping the water, he is using a ‘positive hook angle’, but if the hand is laid back and just slapping water, it is a ‘negative hook angle’ effect. The swimmer won’t go anywhere using a ‘negative hook’ hand angle, but such is not the case with a spinning sawblade. It still cuts just fine when a negative hook angle is used, but because it is not digging or scooping, the operator has maximum control over the head and blade.
High-speed steel sawblades (those without carbide tips) are not really described in terms of ‘hook angles’ because a HSS blade truly cuts through the wood, whereas a carbide-tipped blade ‘scrapes’ its way thru.
Years ago, on any saw where the blade was suspended over the workpiece (ex: a miter saw; Delta’s “Sawbuck”, a sliding miter saw, or even a sliding compound miter saw) one would never see any blade on it, other than a negative hook. For some reason, that has changed. Now, one might see a 12 to 15degree positive hook blade installed on one of these saws, right out of the factory. While I am not going to speculate as to why the manufacturer’s decided that they could do this, I will say that I, personally, am not comfortable with it. As I told about in my example of testing, a negative hook blade offers the user so much more control over the sliding head, that to use any positive hook blade just invites ‘climb-cutting’.
On miter saws, where the head does not slide, a positive hook blade could be used and it still be as safe as using it in a table saw (which is another discussion entirely) because the head is ‘locked in’. There is no sliding movement as there is on a Radial Arm Saw or a sliding miter saw. With this in mind, I can understand it, but on a sliding miter saw? Not for me.
Hopefully, from our discussions, you have a better understanding of some of the techniques of a Radial Arm Saw’s blade needs. Next week, we’ll take a look at the different styles of RAS’s and get a tip or two about how to go about properly aligning a RAS
Send your questions or comments to:
Toolsmartz@bellsouth.net and we’ll see what we can do to help you.
_______________________________________________________________
Any views or opinions presented in this article are solely those of the author and do not necessarily represent those of this newspaper. Neither the author, nor this newspaper, accepts any liability for the content of this article, or for the consequences of any actions taken on the basis of the information provided.
My best description of how to check a sawblade’s hook angle was the ‘intersecting line method’ that I outlined last week. My second-most used visual to help understand this is that of a swimmer’s hand. If the hand is scooping the water, he is using a ‘positive hook angle’, but if the hand is laid back and just slapping water, it is a ‘negative hook angle’ effect. The swimmer won’t go anywhere using a ‘negative hook’ hand angle, but such is not the case with a spinning sawblade. It still cuts just fine when a negative hook angle is used, but because it is not digging or scooping, the operator has maximum control over the head and blade.
High-speed steel sawblades (those without carbide tips) are not really described in terms of ‘hook angles’ because a HSS blade truly cuts through the wood, whereas a carbide-tipped blade ‘scrapes’ its way thru.
Years ago, on any saw where the blade was suspended over the workpiece (ex: a miter saw; Delta’s “Sawbuck”, a sliding miter saw, or even a sliding compound miter saw) one would never see any blade on it, other than a negative hook. For some reason, that has changed. Now, one might see a 12 to 15degree positive hook blade installed on one of these saws, right out of the factory. While I am not going to speculate as to why the manufacturer’s decided that they could do this, I will say that I, personally, am not comfortable with it. As I told about in my example of testing, a negative hook blade offers the user so much more control over the sliding head, that to use any positive hook blade just invites ‘climb-cutting’.
On miter saws, where the head does not slide, a positive hook blade could be used and it still be as safe as using it in a table saw (which is another discussion entirely) because the head is ‘locked in’. There is no sliding movement as there is on a Radial Arm Saw or a sliding miter saw. With this in mind, I can understand it, but on a sliding miter saw? Not for me.
Hopefully, from our discussions, you have a better understanding of some of the techniques of a Radial Arm Saw’s blade needs. Next week, we’ll take a look at the different styles of RAS’s and get a tip or two about how to go about properly aligning a RAS
Send your questions or comments to:
Toolsmartz@bellsouth.net and we’ll see what we can do to help you.
_______________________________________________________________
Any views or opinions presented in this article are solely those of the author and do not necessarily represent those of this newspaper. Neither the author, nor this newspaper, accepts any liability for the content of this article, or for the consequences of any actions taken on the basis of the information provided.
#34- Radial Arm Saw- How’s your Hook?
Last week, we started a discussion about the Radial Arm Saw and I covered a couple of the reasons as to why I am a member of the ‘pull the blade through the workpiece’ camp. We’ll continue the discussion this week with reason #3.
Third, IF the proper negative-hook sawblade is used, the operator has complete control over the force of the blade thru the wood. Now, IF a positive-hook blade is used, the blade will try to ‘climb’ thru the workpiece and make the operator push back against it. ALWAYS use a negative-hook sawblade on your Radial Arm Saw.
I did some testing years ago and it really is true. Using the ‘pull-through’ method, with a 20 degree positive-hook blade, I had to push back against the saw head slightly to keep the blade from trying to ‘run’ towards me. On the other hand (again using the pull-through method), when I used a 15 degree negative-hook blade, I could use one finger to pull the blade thru the wood and it did not try to climb at all. In fact, I would let the head stop every couple of inches and just let it sit there…and it wouldn’t move, even though the blade was spinning at 3450rpm and buried in the wood.
This might be a good place for a talk about negative and positive blade “hook angles” because they do have an effect on how smoothly a RAS blade can pass thru a workpiece. For this discussion, we are talking about carbide tipped blades. Picture, if you will, a circle. On that circle, we draw a straight line vertically and a straight line horizontally - with the intersection of the two lines dead center in the middle of the blade’s hole. Now, we give that circle some blade teeth and let’s say that the ‘blade’ is going to rotate, and cut, counter-clockwise. Align one particular tooth right on the vertical line.
With that picture firmly in mind, here are your three ‘hook angle’ definitions:
If the flat of a tooth is exactly aligned with the vertical line, that blade is a ‘zero hook angle’ blade.
If the flat of the tooth has its upper tip tilted in the cutting direction (in our example, that would be counter-clockwise) this blade is a ’Positive hook angle’ blade.
If the flat of the tooth has its upper tip tilted AWAY from the cutting direction (in our example, that would be counter-clockwise) this blade is a ’Negative hook angle’ blade.
We’ll pick up here, next week.
Send your questions or comments to:
Toolsmartz@bellsouth.net and we’ll see what we can do to help you.
_______________________________________________________________
Any views or opinions presented in this article are solely those of the author and do not necessarily represent those of this newspaper. Neither the author, nor this newspaper, accepts any liability for the content of this article, or for the consequences of any actions taken on the basis of the information provided.
Third, IF the proper negative-hook sawblade is used, the operator has complete control over the force of the blade thru the wood. Now, IF a positive-hook blade is used, the blade will try to ‘climb’ thru the workpiece and make the operator push back against it. ALWAYS use a negative-hook sawblade on your Radial Arm Saw.
I did some testing years ago and it really is true. Using the ‘pull-through’ method, with a 20 degree positive-hook blade, I had to push back against the saw head slightly to keep the blade from trying to ‘run’ towards me. On the other hand (again using the pull-through method), when I used a 15 degree negative-hook blade, I could use one finger to pull the blade thru the wood and it did not try to climb at all. In fact, I would let the head stop every couple of inches and just let it sit there…and it wouldn’t move, even though the blade was spinning at 3450rpm and buried in the wood.
This might be a good place for a talk about negative and positive blade “hook angles” because they do have an effect on how smoothly a RAS blade can pass thru a workpiece. For this discussion, we are talking about carbide tipped blades. Picture, if you will, a circle. On that circle, we draw a straight line vertically and a straight line horizontally - with the intersection of the two lines dead center in the middle of the blade’s hole. Now, we give that circle some blade teeth and let’s say that the ‘blade’ is going to rotate, and cut, counter-clockwise. Align one particular tooth right on the vertical line.
With that picture firmly in mind, here are your three ‘hook angle’ definitions:
If the flat of a tooth is exactly aligned with the vertical line, that blade is a ‘zero hook angle’ blade.
If the flat of the tooth has its upper tip tilted in the cutting direction (in our example, that would be counter-clockwise) this blade is a ’Positive hook angle’ blade.
If the flat of the tooth has its upper tip tilted AWAY from the cutting direction (in our example, that would be counter-clockwise) this blade is a ’Negative hook angle’ blade.
We’ll pick up here, next week.
Send your questions or comments to:
Toolsmartz@bellsouth.net and we’ll see what we can do to help you.
_______________________________________________________________
Any views or opinions presented in this article are solely those of the author and do not necessarily represent those of this newspaper. Neither the author, nor this newspaper, accepts any liability for the content of this article, or for the consequences of any actions taken on the basis of the information provided.
#33- The mysterious Radial Arm Saw
OK, let’s get back to the task of learning more about our many shop tools and machines. This week, we’ll take a look at one of the most versatile machines, but also one of the most dangerous.
The Radial Arm Saw. Sometimes, the very words can make a grizzled woodworking veteran recheck his hands to make sure he still has all of his fingers and thumbs. This machine requires THAT much caution when using it.
But, as with most machines, if you respect it and realize what it can do to you in a heartbeat… you simply must be careful.
Just so that we are all on the same page, let’s outline a few parts of the saw.
The “head” is the part of the saw that holds the “sawblade” and slides fore and aft on the “track”. The “track” is the “arm” of the saw that holds the “head”, which is sometimes also called the “carriage”. The “fence” is the barrier that the workpiece is held against while laying on the “table” which references the workpiece, prior to being cut. The “off” position of the head/blade is when the head is fully retracted towards the rear of the saw, behind the fence.
Alright, now let’s take a look at one of the more frequent questions that I’ve been asked: “Should I pull the blade thru the wood, or push it through?” While I am sure that I may get some pushback, I will state my case and the reasons that I believe as I do. In my opinion, the blade should be pulled thru the workpiece. Here’s why.
First, when the blade and head are at rest, they are retracted behind the fence, away from the operator. That is a good position to then start the saw up, without it being hung out in space next to the operator.
Second, the proper blade rotation is over the top towards the operator, and down and under and away from the operator. Given this, if the head is retracted behind the fence and turned on, then pulled into the wood, the first contact the blade has with the stock will be pushing the stock down into the table and towards the fence. That places all of the cutting force downward towards the table, and rearwards towards the fence – both are very good things because they properly brace the workpiece.
If the blade were to be pushed into the stock, the first blade contact would tend to lift the workpiece…NOT good.
Next week, we’ll tell you more about the Radial Arm Saw.
Send your questions or comments to:
Toolsmartz@bellsouth.net and we’ll see what we can do to help you.
_______________________________________________________________
Any views or opinions presented in this article are solely those of the author and do not necessarily represent those of this newspaper. Neither the author, nor this newspaper, accepts any liability for the content of this article, or for the consequences of any actions taken on the basis of the information provided.
The Radial Arm Saw. Sometimes, the very words can make a grizzled woodworking veteran recheck his hands to make sure he still has all of his fingers and thumbs. This machine requires THAT much caution when using it.
But, as with most machines, if you respect it and realize what it can do to you in a heartbeat… you simply must be careful.
Just so that we are all on the same page, let’s outline a few parts of the saw.
The “head” is the part of the saw that holds the “sawblade” and slides fore and aft on the “track”. The “track” is the “arm” of the saw that holds the “head”, which is sometimes also called the “carriage”. The “fence” is the barrier that the workpiece is held against while laying on the “table” which references the workpiece, prior to being cut. The “off” position of the head/blade is when the head is fully retracted towards the rear of the saw, behind the fence.
Alright, now let’s take a look at one of the more frequent questions that I’ve been asked: “Should I pull the blade thru the wood, or push it through?” While I am sure that I may get some pushback, I will state my case and the reasons that I believe as I do. In my opinion, the blade should be pulled thru the workpiece. Here’s why.
First, when the blade and head are at rest, they are retracted behind the fence, away from the operator. That is a good position to then start the saw up, without it being hung out in space next to the operator.
Second, the proper blade rotation is over the top towards the operator, and down and under and away from the operator. Given this, if the head is retracted behind the fence and turned on, then pulled into the wood, the first contact the blade has with the stock will be pushing the stock down into the table and towards the fence. That places all of the cutting force downward towards the table, and rearwards towards the fence – both are very good things because they properly brace the workpiece.
If the blade were to be pushed into the stock, the first blade contact would tend to lift the workpiece…NOT good.
Next week, we’ll tell you more about the Radial Arm Saw.
Send your questions or comments to:
Toolsmartz@bellsouth.net and we’ll see what we can do to help you.
_______________________________________________________________
Any views or opinions presented in this article are solely those of the author and do not necessarily represent those of this newspaper. Neither the author, nor this newspaper, accepts any liability for the content of this article, or for the consequences of any actions taken on the basis of the information provided.
#32 - Reviving The Dead Hot Rod - part 3
Picking up from last week… the little ’34 Ford coupe is painted and suffering from a worn out coil. Run it until it gets warm and it’ll stop working until it cools off. We finally decided to make a homemade adaptor to be able to use a new coil (we didn’t even know enough to realize that somebody, somewhere probably made new ones). So, the car runs and I go into the Navy for a few years. For some reason, dad just never again had any desire to drive the coupe around- so every time I’d come home on leave, I’d charge the battery, drive her around a bit and then park it until next time.
In 1996, dad finally decided to put hydraulic brakes on it. He found a good deal on some parts in Halls, TN that would make the job fairly easy…and guess who got commissioned to do the work? His one and only son, me.
Well, we changed the front end, the rearend, ran hydraulic lines and fabricated a mount for the master cylinder. It did stop better after that.
But after that spurt, she went right back into the garage. It’s really amazing what damage a car can suffer just simply sitting in a garage. Things fall over on it, stuff gets spilled on the fenders and dust grows by the pound. It sounds bad, but it really gave the little car some ‘character’…like it had been used all those years. It’s a secret that only we know.
Well, time does pass and one day in 2001, I was visiting dad and he asked me for a dollar. Sure I asked for what, but he hounded me until I gave him one and he handed me the title to the coupe. Wow. Now I had my own real Hot Rod.
Since then I have tried to make the car as safe as possible and look like it was built in the 50’s. I changed the electric system to 12 volt, split the front wishbone, added tube shocks, put in safety belts, changed to late model wire wheels and radial tires, revived a 2 carb intake that dad used to run on his dirt track race car in the late 50’s, got a new radiator and electric fan and installed a set of finned aluminum heads. Without the hood is my chosen method of running it, and it really looks like it would do a hundred miles an hour.
Keep an eye out for us around the ‘boro and if you see us, honk & wave. We spend a lot of time at our AACA club’s garage down in Cannonsburgh.
In 1996, dad finally decided to put hydraulic brakes on it. He found a good deal on some parts in Halls, TN that would make the job fairly easy…and guess who got commissioned to do the work? His one and only son, me.
Well, we changed the front end, the rearend, ran hydraulic lines and fabricated a mount for the master cylinder. It did stop better after that.
But after that spurt, she went right back into the garage. It’s really amazing what damage a car can suffer just simply sitting in a garage. Things fall over on it, stuff gets spilled on the fenders and dust grows by the pound. It sounds bad, but it really gave the little car some ‘character’…like it had been used all those years. It’s a secret that only we know.
Well, time does pass and one day in 2001, I was visiting dad and he asked me for a dollar. Sure I asked for what, but he hounded me until I gave him one and he handed me the title to the coupe. Wow. Now I had my own real Hot Rod.
Since then I have tried to make the car as safe as possible and look like it was built in the 50’s. I changed the electric system to 12 volt, split the front wishbone, added tube shocks, put in safety belts, changed to late model wire wheels and radial tires, revived a 2 carb intake that dad used to run on his dirt track race car in the late 50’s, got a new radiator and electric fan and installed a set of finned aluminum heads. Without the hood is my chosen method of running it, and it really looks like it would do a hundred miles an hour.
Keep an eye out for us around the ‘boro and if you see us, honk & wave. We spend a lot of time at our AACA club’s garage down in Cannonsburgh.
Monday, September 6, 2010
#31- Reviving The Dead Hot Rod - part 2
Picking up from last week… the little ’34 Ford coupe is sitting in our backyard in Memphis, and has been for 9 years. It was my junior year in high school and the 1st Street Rod Nationals, for cars built in 1948 or earlier, had been held in Peoria, IL in 1970. I read all about it Rod & Custom magazine, but of course, I wasn’t there…Well, lo & behold, in 1971 the 2nd Street Rod Nationals came to the bluff city. I drove down to Highland Ave at night and all those Hot Rods and beautiful cars in the street lights was a sight to see. I was in ‘car nut’ heaven!
So, I’m hanging out checking out all those hot rods and thinking “Wow, I wish I had a car like these…HOLD IT!...There’s one of them in our back yard!!!” So, over the next few weeks, I talked my dad into footing the bills and me doing the labor to fix up the old ’34 and he agreed.
The first thing we did was get the car ready for the engine and believe it or not, when we went to my dad’s friend’s garage, the fresh 1936 motor was still there in it’s plastic bag. We towed the car up there and used his engine hoist to put the motor back in the car. Over the next few weeks, we got the motor running - fall of 1971.
That turned out to be the easy part. Mechanically, I am a wiz, but I found out real quick that body work is not my strong suit. I just don’t have the ‘touch’. I can lay down paint with the best of them, but don’t ask me to smooth out a body panel…even now, when people see the car, I tell them “If the body work looks like a 16 year old kid did it…it was me”. Over the course of the next 2 years, I disassembled the car, right down to the point of removing the body from the frame. We didn’t do that because we had no garage to store it in. But we had the fenders off and sanded everything down to bare metal so that we could put lacquer paint back on it.
By the summer of 1973, we had painted the car black & yellow and we had figured out that the distributor coil was bad. It would run fine until the coil got hot and then it would leave you stranded until it cooled down.
Next week, we’ll finish up the story of the Hot Rod.
So, I’m hanging out checking out all those hot rods and thinking “Wow, I wish I had a car like these…HOLD IT!...There’s one of them in our back yard!!!” So, over the next few weeks, I talked my dad into footing the bills and me doing the labor to fix up the old ’34 and he agreed.
The first thing we did was get the car ready for the engine and believe it or not, when we went to my dad’s friend’s garage, the fresh 1936 motor was still there in it’s plastic bag. We towed the car up there and used his engine hoist to put the motor back in the car. Over the next few weeks, we got the motor running - fall of 1971.
That turned out to be the easy part. Mechanically, I am a wiz, but I found out real quick that body work is not my strong suit. I just don’t have the ‘touch’. I can lay down paint with the best of them, but don’t ask me to smooth out a body panel…even now, when people see the car, I tell them “If the body work looks like a 16 year old kid did it…it was me”. Over the course of the next 2 years, I disassembled the car, right down to the point of removing the body from the frame. We didn’t do that because we had no garage to store it in. But we had the fenders off and sanded everything down to bare metal so that we could put lacquer paint back on it.
By the summer of 1973, we had painted the car black & yellow and we had figured out that the distributor coil was bad. It would run fine until the coil got hot and then it would leave you stranded until it cooled down.
Next week, we’ll finish up the story of the Hot Rod.
#30- The Hot Rod Detour- part 1
I think we’ll take a ‘detour’ this week and let you know more about my other passion - aside from the care and feeding of woodworking machines and Taylor-Tot strollers. I love Hot Rods - Ol’ Skool, fire-breathing Hot Rods.
You might recognize those words from column #13, but they sounded so good, I decided to use them again and let you know a bit more about our 1934 Ford coupe’. In the mid 1950’s my dad was a Memphis/Mid-South area truck driver who delivered auto parts to those mom ‘n pop parts stores (that have almost faded away, thanks to AutoZone, Advance, etc…) and he was actively seeking a decent 1934 car because it was the year he was born in.
Well, on one of his trips, he wound up in Greenville, MS and ran across a nice little ’34 Ford. The kid that had it had hit the back end of another car and his mom was making him sell his car…for $100. That was quite a bit of money back in 1958, but dad scraped it together and bought the car in November.
He brought it home and proceeded to use it for driving back and forth to work. At that time he had to get up around 4am and I remember my mom getting up many a morning to push him down the street, so the ’34 would start. Around 1962, the motor’s block cracked and needed to be replaced. Dad pulled the engine out and during one of his runs to Blytheville, Arkansas, he found a freshly rebuilt 1936 short block for $50. (yes, ½ the price he paid for the whole car) The ’36 motor is better because it has insert bearings. The original ’34 motor uses babbited bearings, which is much harder to repair, if need be.
Anyway, he purchased the rebuilt block and brought it home, but since we didn’t have a garage at the time, he took it to a friend who lived in the next block and stored it in his garage.
Well, time moves along and one thing led to another and after 9 years, that motor still sat in his friend’s garage, and the ’34 still sat in our backyard without a motor. Yes, I had gotten in trouble a few times for ’playing’ on it, and there is no telling how many people stopped by our house to see about buying the little coupe...no matter how hard we tried to hide it from view of the road. Dad never sold it. Next week, I’ll tell you how it came back from the dead…’til then.
You might recognize those words from column #13, but they sounded so good, I decided to use them again and let you know a bit more about our 1934 Ford coupe’. In the mid 1950’s my dad was a Memphis/Mid-South area truck driver who delivered auto parts to those mom ‘n pop parts stores (that have almost faded away, thanks to AutoZone, Advance, etc…) and he was actively seeking a decent 1934 car because it was the year he was born in.
Well, on one of his trips, he wound up in Greenville, MS and ran across a nice little ’34 Ford. The kid that had it had hit the back end of another car and his mom was making him sell his car…for $100. That was quite a bit of money back in 1958, but dad scraped it together and bought the car in November.
He brought it home and proceeded to use it for driving back and forth to work. At that time he had to get up around 4am and I remember my mom getting up many a morning to push him down the street, so the ’34 would start. Around 1962, the motor’s block cracked and needed to be replaced. Dad pulled the engine out and during one of his runs to Blytheville, Arkansas, he found a freshly rebuilt 1936 short block for $50. (yes, ½ the price he paid for the whole car) The ’36 motor is better because it has insert bearings. The original ’34 motor uses babbited bearings, which is much harder to repair, if need be.
Anyway, he purchased the rebuilt block and brought it home, but since we didn’t have a garage at the time, he took it to a friend who lived in the next block and stored it in his garage.
Well, time moves along and one thing led to another and after 9 years, that motor still sat in his friend’s garage, and the ’34 still sat in our backyard without a motor. Yes, I had gotten in trouble a few times for ’playing’ on it, and there is no telling how many people stopped by our house to see about buying the little coupe...no matter how hard we tried to hide it from view of the road. Dad never sold it. Next week, I’ll tell you how it came back from the dead…’til then.
Saturday, August 28, 2010
#29 - Bench Grinder: Tips & Techniques
We’ll finish up our look at Bench Grinders with a few Tips & Techniques.
Every once in a while, we run across something new about Bench Grinders, but most of our knowledge is tried & true, and time-tested.
First off, every ‘store-bought’ grinding wheel that I know of has blotters on its sides. ‘Blotters’ are those pieces of paper, or cardboard, on each side of the wheel. While they might look like just a convenient place for the manufacturer to put warnings and such, they actually do serve a very critical purpose. When a wheel is put on a grinder, there are metal flanges that squeeze against the sides of the wheel. If the wheel had no blotters, those flanges would be tightening up against the actual rock of the wheel and you would stand a very good chance of cracking the wheel. Blotters provide a ‘buffer’ between the flanges and the wheel rock and thereby cushion and distribute the tightening force. Bottom line: Don’t buy a wheel that has no blotters or, if you do, don’t put it on your grinder without making some blotters and using them.
While we’re talking about blotters, they have another use. Most manufacturers put their product warnings on them and one of the major warnings is “Do not grind on side of wheel”. Now, do most of us follow this warning? Probably not, but I am here to tell you that if enough sideways force is applied to as grinding wheel, a wheel explosion is a very real possibility. Years ago, I saw a training film (yes, “film”- not tape or DVD- I’m dating myself) wherein a grinding wheel explosion was created and it is not a pretty sight. Even though I might use the side of the wheel to do some very light & delicate, precise grinding, I’m only able to do so because of my many years of experience with this and I know that I am not applying any sideways force at all. My general advice to everyone is: Don’t grind on the side of the wheel.
Lastly, always keep the tool rest adjusted as close to the wheel as possible, in order to provide the most support for what you are grinding on. Use your safety glasses. Keep the grinder’s eyeshield in place to provide added protection. Make sure the spark arrester is in place and adjusted to within 1/8” of the wheel and always keep an open container of water handy for cooling off your material. If your grinder has a factory water pot, that’s even better. Keep it full.
These hints, and our last two columns, should help you get the most out of your Bench Grinder. Happy Grinding!
Every once in a while, we run across something new about Bench Grinders, but most of our knowledge is tried & true, and time-tested.
First off, every ‘store-bought’ grinding wheel that I know of has blotters on its sides. ‘Blotters’ are those pieces of paper, or cardboard, on each side of the wheel. While they might look like just a convenient place for the manufacturer to put warnings and such, they actually do serve a very critical purpose. When a wheel is put on a grinder, there are metal flanges that squeeze against the sides of the wheel. If the wheel had no blotters, those flanges would be tightening up against the actual rock of the wheel and you would stand a very good chance of cracking the wheel. Blotters provide a ‘buffer’ between the flanges and the wheel rock and thereby cushion and distribute the tightening force. Bottom line: Don’t buy a wheel that has no blotters or, if you do, don’t put it on your grinder without making some blotters and using them.
While we’re talking about blotters, they have another use. Most manufacturers put their product warnings on them and one of the major warnings is “Do not grind on side of wheel”. Now, do most of us follow this warning? Probably not, but I am here to tell you that if enough sideways force is applied to as grinding wheel, a wheel explosion is a very real possibility. Years ago, I saw a training film (yes, “film”- not tape or DVD- I’m dating myself) wherein a grinding wheel explosion was created and it is not a pretty sight. Even though I might use the side of the wheel to do some very light & delicate, precise grinding, I’m only able to do so because of my many years of experience with this and I know that I am not applying any sideways force at all. My general advice to everyone is: Don’t grind on the side of the wheel.
Lastly, always keep the tool rest adjusted as close to the wheel as possible, in order to provide the most support for what you are grinding on. Use your safety glasses. Keep the grinder’s eyeshield in place to provide added protection. Make sure the spark arrester is in place and adjusted to within 1/8” of the wheel and always keep an open container of water handy for cooling off your material. If your grinder has a factory water pot, that’s even better. Keep it full.
These hints, and our last two columns, should help you get the most out of your Bench Grinder. Happy Grinding!
#28 - Dressing your Bench Grinder wheels
Last week we talked about one of the staples in every shop, the Bench Grinder. This week, we’ll continue that theme and talk about the ‘care & feeding’ of your grinder.
Just for a bit of clarification from last week, my point about using a slow speed grinder (which is what a 1725rpm grinder is called in the industry) is that one needs to be careful when grinding metal and not heat the metal up too much. With a slow speed grinder, it is much easier to keep the grinding heat under control.
Ok, let’s talk about one of the natural problems with any grinder. After some grinding time, the face of the wheel will get ridges, or become tapered and one must “re-face” the wheel to get back to a smooth grinding surface. There are a couple of ways to do this.
Some grinders, the more professional models, usually have an accessory that is used to re-face the wheels. It bolts on in place of the tool rest and uses a diamond-tipped tool to re-face the wheel. Having one of these makes the task much easier. Unfortunately, not all grinders offer that. If your grinder isn’t that sophisticated, just buy the diamond-tipped tool and use it free-hand. The technique is not that hard to learn, in fact, if you have had enough grinding experience to get your wheel out of shape, you certainly have enough experience to re-face it.
So, let’s say that you don’t have the re-facing accessory and you must do it free-hand. The diamond-tipped facing tool I am most familiar with has a round shank, so that is what I will speak to. The technique is to place the tool on the tool rest as if you were trying to grind the diamond off of the end. Support it very well with your hands. In fact the tighter you hold it, and control it, the straighter your face finish will be.
Make sure you have your safety glasses on, and turn the grinder on. Put the tool on the tool rest. You would let the diamond tip touch the face of the wheel very lightly- you do not want to ‘deep grind’ this- and move the tool side to side as straight, and smooth, as possible. Keep the tool at 90degrees to the face of the wheel and realize that the high points of the wheel face will require a lot of material removal before you will get close to having a straight wheel face again. With patience and a bit of time, you will again have a smooth wheel face to use.
Just for a bit of clarification from last week, my point about using a slow speed grinder (which is what a 1725rpm grinder is called in the industry) is that one needs to be careful when grinding metal and not heat the metal up too much. With a slow speed grinder, it is much easier to keep the grinding heat under control.
Ok, let’s talk about one of the natural problems with any grinder. After some grinding time, the face of the wheel will get ridges, or become tapered and one must “re-face” the wheel to get back to a smooth grinding surface. There are a couple of ways to do this.
Some grinders, the more professional models, usually have an accessory that is used to re-face the wheels. It bolts on in place of the tool rest and uses a diamond-tipped tool to re-face the wheel. Having one of these makes the task much easier. Unfortunately, not all grinders offer that. If your grinder isn’t that sophisticated, just buy the diamond-tipped tool and use it free-hand. The technique is not that hard to learn, in fact, if you have had enough grinding experience to get your wheel out of shape, you certainly have enough experience to re-face it.
So, let’s say that you don’t have the re-facing accessory and you must do it free-hand. The diamond-tipped facing tool I am most familiar with has a round shank, so that is what I will speak to. The technique is to place the tool on the tool rest as if you were trying to grind the diamond off of the end. Support it very well with your hands. In fact the tighter you hold it, and control it, the straighter your face finish will be.
Make sure you have your safety glasses on, and turn the grinder on. Put the tool on the tool rest. You would let the diamond tip touch the face of the wheel very lightly- you do not want to ‘deep grind’ this- and move the tool side to side as straight, and smooth, as possible. Keep the tool at 90degrees to the face of the wheel and realize that the high points of the wheel face will require a lot of material removal before you will get close to having a straight wheel face again. With patience and a bit of time, you will again have a smooth wheel face to use.
#27 - A shop ‘must have’: The Bench Grinder
I would wager that most anyone who has a shop, or works in one, would be among the first to tell you that one of the most necessary tools in their shop would be their bench grinder. This may not apply for some specific woodshops, but since Toolsmartz is about ALL shops, we can cover it.
Bench grinders come in many different sizes and the major defining factor about them is the wheel diameter. Most people would not say, ‘yea, I have a ½ horsepower bench grinder’. No, they will be saying, ‘yea, I have an 8” bench grinder’. Even the bench grinder manufacturers set up their advertising literature in this fashion. The grinder’s horsepower and speed are somewhat of a secondary matter, after the wheel diameter, but don’t mis-understand, the horsepower and speed are critical factors when selecting the correct bench grinder, but what is usually seen is that as the wheel diameter gets larger, so does the horsepower. This allows the bench grinder to tackle harder jobs.
The deal is, when you have a large item to grind on, you really need a decent sized bench grinder. My personal philosophy is that if you have a large (meaning 10” wheels) bench grinder and need to do a small job, it can handle it. On the other hand if you have a small (meaning 4” or 6” wheels) bench grinder and need to do a big job, you can’t…or if you try to, you may burn up your small grinder. So yes, when considering what bench grinder to choose, size does matter.
Another factor to consider is the bench grinder’s speed. This is also known as the RPM of the grinder. For most grinding operations, I prefer a speed of 1725RPM. Many grinders only come in a speed of 3450RPM, which is fine for many operations, but again, if you have a 1725RPM speed, you can pretty much always do whatever it is that you need to do. If you only have a 3450RPM grinder, I can promise you that you will overheat some items real fast.
As I suppose you have gathered, my personal favorite bench grinder is my 10”, 1725RPM unit. It has no problem grinding small parts and it can handle all of my lawnmower blades without overheating them and burning them up.
Next week, we’ll continue this Bench Grinder discussion and get into some of the typical problems that you might encounter and recommendations for solving them.
Bench grinders come in many different sizes and the major defining factor about them is the wheel diameter. Most people would not say, ‘yea, I have a ½ horsepower bench grinder’. No, they will be saying, ‘yea, I have an 8” bench grinder’. Even the bench grinder manufacturers set up their advertising literature in this fashion. The grinder’s horsepower and speed are somewhat of a secondary matter, after the wheel diameter, but don’t mis-understand, the horsepower and speed are critical factors when selecting the correct bench grinder, but what is usually seen is that as the wheel diameter gets larger, so does the horsepower. This allows the bench grinder to tackle harder jobs.
The deal is, when you have a large item to grind on, you really need a decent sized bench grinder. My personal philosophy is that if you have a large (meaning 10” wheels) bench grinder and need to do a small job, it can handle it. On the other hand if you have a small (meaning 4” or 6” wheels) bench grinder and need to do a big job, you can’t…or if you try to, you may burn up your small grinder. So yes, when considering what bench grinder to choose, size does matter.
Another factor to consider is the bench grinder’s speed. This is also known as the RPM of the grinder. For most grinding operations, I prefer a speed of 1725RPM. Many grinders only come in a speed of 3450RPM, which is fine for many operations, but again, if you have a 1725RPM speed, you can pretty much always do whatever it is that you need to do. If you only have a 3450RPM grinder, I can promise you that you will overheat some items real fast.
As I suppose you have gathered, my personal favorite bench grinder is my 10”, 1725RPM unit. It has no problem grinding small parts and it can handle all of my lawnmower blades without overheating them and burning them up.
Next week, we’ll continue this Bench Grinder discussion and get into some of the typical problems that you might encounter and recommendations for solving them.
Friday, July 30, 2010
#26 - Drill Press ‘Tips & Techniques’
I thought that for this week, I would just go over some of the little tidbits of information that I like to call ‘Tips & Techniques’. Since we have been discussing Drill Presses the past 2 weeks, we might as well stay on topic.
One of the areas that folks need some assistance with is that of choosing the right DP speed for their particular project. The main rule of thumb is: ‘The harder the material, the slower the bit needs to turn.’ Right behind that comes this: ‘The bigger your bit, the slower it needs to turn’. How that plays out is like this. If you’re drilling the same size hole in wood and metal, the speed will need to be slowed down for drilling into metal. By the same token, if you’re drilling into pine wood and making a ¼” hole and a 2-1/4” hole, slow it down for the 2-1/4” hole. It may be that not much speed change is needed between these two, but the idea is that you don’t usually want a 2-1/4 cutter turning as fast as a small ¼ bit.
Now, let’s talk safety. First and foremost, dress appropriately when using a Drill Press. Wear your safety glasses, roll up your long sleeves and pull your hair back out of the way (IF your hair is that long). I once saw a training film that showed what happened when a lady got her long hair tangled in the Drill Press she was operating. It was not a pretty sight. She reminded me of what Custer’s men must have looked like after being scalped.
After you have all those bases covered, here’s another ‘first and foremost’- ALWAYS clamp your work. I cannot over-emphasize this. Yes, it’s a pain and not always convenient but it IS necessary. I have a nice 2” long scar on my left forearm that is a constant reminder of this. The very afternoon that I was going to drive my dirt track racecar for the first time, I was making an accelerator bracket and need to drill a hole in it. The bracket was just 8” long, ¾” flat stock, with one end bent at a 45 and that was where I needed the hole. So I go to my DP and hold the long part and place the bent area on the table under the bit. I started drilling the hole and OOPS…it grabbed and swung around 360 degrees and in the blink of an eye, it made a few revolutions before I could get it shut off. Unfortunately, on that first swing, the top end of the stock sliced my wrist open and I wear that reminder to this day. It looks like I tried to commit suicide. So, I tell everyone - clamp your stock.
Send your questions or comments to:
Toolsmartz@bellsouth.net and we’ll see what we can do to help you.
_______________________________________________________________
Any views or opinions presented in this article are solely those of the author and do not necessarily represent those of this newspaper. Neither the author, nor this newspaper, accepts any liability for the content of this article, or for the consequences of any actions taken on the basis of the information provided.
One of the areas that folks need some assistance with is that of choosing the right DP speed for their particular project. The main rule of thumb is: ‘The harder the material, the slower the bit needs to turn.’ Right behind that comes this: ‘The bigger your bit, the slower it needs to turn’. How that plays out is like this. If you’re drilling the same size hole in wood and metal, the speed will need to be slowed down for drilling into metal. By the same token, if you’re drilling into pine wood and making a ¼” hole and a 2-1/4” hole, slow it down for the 2-1/4” hole. It may be that not much speed change is needed between these two, but the idea is that you don’t usually want a 2-1/4 cutter turning as fast as a small ¼ bit.
Now, let’s talk safety. First and foremost, dress appropriately when using a Drill Press. Wear your safety glasses, roll up your long sleeves and pull your hair back out of the way (IF your hair is that long). I once saw a training film that showed what happened when a lady got her long hair tangled in the Drill Press she was operating. It was not a pretty sight. She reminded me of what Custer’s men must have looked like after being scalped.
After you have all those bases covered, here’s another ‘first and foremost’- ALWAYS clamp your work. I cannot over-emphasize this. Yes, it’s a pain and not always convenient but it IS necessary. I have a nice 2” long scar on my left forearm that is a constant reminder of this. The very afternoon that I was going to drive my dirt track racecar for the first time, I was making an accelerator bracket and need to drill a hole in it. The bracket was just 8” long, ¾” flat stock, with one end bent at a 45 and that was where I needed the hole. So I go to my DP and hold the long part and place the bent area on the table under the bit. I started drilling the hole and OOPS…it grabbed and swung around 360 degrees and in the blink of an eye, it made a few revolutions before I could get it shut off. Unfortunately, on that first swing, the top end of the stock sliced my wrist open and I wear that reminder to this day. It looks like I tried to commit suicide. So, I tell everyone - clamp your stock.
Send your questions or comments to:
Toolsmartz@bellsouth.net and we’ll see what we can do to help you.
_______________________________________________________________
Any views or opinions presented in this article are solely those of the author and do not necessarily represent those of this newspaper. Neither the author, nor this newspaper, accepts any liability for the content of this article, or for the consequences of any actions taken on the basis of the information provided.
Monday, July 26, 2010
New adventures on the horizon
I am PUMPED.
I have accepted a new position with National Pen Co. In Shelbyville, TN and I start next Monday (8-2). This is the first job that I have taken in over 3 years that I truly feel is a solid fit for my skills. I KNOW how to take care of my customers and that is what I will be doing for National Pen.
Please join me in prayer that I will exceed my employer's expectations and that they will recognize my abilities and potential.
I have accepted a new position with National Pen Co. In Shelbyville, TN and I start next Monday (8-2). This is the first job that I have taken in over 3 years that I truly feel is a solid fit for my skills. I KNOW how to take care of my customers and that is what I will be doing for National Pen.
Please join me in prayer that I will exceed my employer's expectations and that they will recognize my abilities and potential.
Thursday, July 22, 2010
#25 - Keeping your Drill Press ‘chucked up’: part 2
Last week we talked about putting your drill chuck on your Drill Press. I ran out of room to fully explore the subject, so here we go again.
Let’s say that you get the chuck installed and all appears to be well. But then, one day, you turn your DP on and the chuck falls off of the spindle nose. Now, what to do?
Well first, you’d want to make sure that the inside of the chuck taper is clean and free from any oil or contaminants. Once you’ve checked/cleaned the chuck, check/clean the spindle nose also.
NOTE: while you are checking/cleaning those tapers, this is a good time to inspect the surface of the tapers closely. The tapers need to be smooth and free from any galling. ‘Galling’ is a machinists term that refers to the tendency of metals, scrubbing together under force, to grind and scar each other. If your chuck has been loose on the spindle nose (unknown to you) for a while, the two parts may have galled their surfaces. IF they have, it is usually useless to try to get them to properly seat again. (The prescription is to replace both parts and start fresh.)
Ok, let’s say that you’ve checked for galling and found both the chuck and the spindle nose to be smooth and in good shape. Now, you’ve cleaned them again and they are now absolutely oil-free and dry as a bone. Take the chuck and ram it sharply onto the spindle nose.
Now, it’s time for the 2x4 and small sledge hammer again. Swing the table out of the way so that you can get a pretty decent swing with your sledge. Retract the chuck jaws to prevent them from getting bent and put your 2x4 under the chuck. Hold the 2x4 with your ‘weak’ hand and use your dominant hand to swing that sledge upward and SMACK the 2x4 (which is against the chuck) very hard.
As I said last week, Tapers seat best with a shock to them. A good 3lb sledge and a 2x4 block will allow you to deliver that shock to the chuck without risking damage to your chuck or Drill Press.
If you continue to have your chuck fall off, there may be a misfit between the two parts, or you may be asking the Drill Press to do something it was not designed to do (like milling, or using an out of balance item in the chuck) and the design of the chuck/spindle taper was not intended to account for that.
Let’s say that you get the chuck installed and all appears to be well. But then, one day, you turn your DP on and the chuck falls off of the spindle nose. Now, what to do?
Well first, you’d want to make sure that the inside of the chuck taper is clean and free from any oil or contaminants. Once you’ve checked/cleaned the chuck, check/clean the spindle nose also.
NOTE: while you are checking/cleaning those tapers, this is a good time to inspect the surface of the tapers closely. The tapers need to be smooth and free from any galling. ‘Galling’ is a machinists term that refers to the tendency of metals, scrubbing together under force, to grind and scar each other. If your chuck has been loose on the spindle nose (unknown to you) for a while, the two parts may have galled their surfaces. IF they have, it is usually useless to try to get them to properly seat again. (The prescription is to replace both parts and start fresh.)
Ok, let’s say that you’ve checked for galling and found both the chuck and the spindle nose to be smooth and in good shape. Now, you’ve cleaned them again and they are now absolutely oil-free and dry as a bone. Take the chuck and ram it sharply onto the spindle nose.
Now, it’s time for the 2x4 and small sledge hammer again. Swing the table out of the way so that you can get a pretty decent swing with your sledge. Retract the chuck jaws to prevent them from getting bent and put your 2x4 under the chuck. Hold the 2x4 with your ‘weak’ hand and use your dominant hand to swing that sledge upward and SMACK the 2x4 (which is against the chuck) very hard.
As I said last week, Tapers seat best with a shock to them. A good 3lb sledge and a 2x4 block will allow you to deliver that shock to the chuck without risking damage to your chuck or Drill Press.
If you continue to have your chuck fall off, there may be a misfit between the two parts, or you may be asking the Drill Press to do something it was not designed to do (like milling, or using an out of balance item in the chuck) and the design of the chuck/spindle taper was not intended to account for that.
#24 - Keeping your Drill Press ‘chucked up’
Well, Mrs. Mayberry is doing good and you all know a lot more about her now, than you did. After a short commercial, let’s get back on the Tooltrack this week. Your columnist is always networking and open to new career opportunities. You can find me on LinkedIn: http://www.linkedin.com/in/tommurrah and I’d be happy to talk with you. If you’re aware of something, drop me a note and we’ll connect.
Now, what about Drill Press chucks?
I was one of those ‘poor folks’ who didn’t have a drill press during my ‘learning how to work on stuff’ years and let me tell you what, by the time I got older and realized what I had been missing…Hoo-boy, was life in the shop so much easier with one around.
Most of today’s ‘home/hobbyist’ drill presses use a taper to hold the chuck onto the spindle. Some manufacturers have the chuck already installed, while others ask the buyer to do it. In any event, the following information will come in handy.
Drill Press Tapers & Chucks usually fall into one of two categories: A spindle with a male taper and the chuck having a female taper; or a spindle with a female taper, a chuck with a female taper and an adapter with a male taper on each end that goes between the chuck and spindle. Each style has their place, with the adaptor style being used more on the bigger Presses.
Alright, there’s your ‘taper background’, now let’s get specific. Drill Press tapers engage (‘seat’) best with a shock. I know some manufacturers who tell you to just push them together, but that’s not the best way. Let’s say that you have a Drill Press with a female tapered chuck and the spindle has the male taper sticking down. First, clean the tapers completely to remove any oil, grease or coating that could prevent metal on metal contact. My favorite solution to this is an old rag saturated with acetone (NOTE: if you use acetone, be aware that it is highly combustible). Next, once the tapers are cleaned, turn the chuck so as to retract the chuck jaws. Next, Place the chuck onto the spindle taper by hand. Finally comes the ‘shock’ part. Put a small 2X4 underneath the chuck jaw opening and use a small mallet (I have a 3lb sledge for this) to hit upward on the 2X4 (chuck bottom). One good sharp whack ought to do it.
Once the tapers are seated properly, they will usually remain engaged unless something too large or out of balance is put into the chuck.
Now, what about Drill Press chucks?
I was one of those ‘poor folks’ who didn’t have a drill press during my ‘learning how to work on stuff’ years and let me tell you what, by the time I got older and realized what I had been missing…Hoo-boy, was life in the shop so much easier with one around.
Most of today’s ‘home/hobbyist’ drill presses use a taper to hold the chuck onto the spindle. Some manufacturers have the chuck already installed, while others ask the buyer to do it. In any event, the following information will come in handy.
Drill Press Tapers & Chucks usually fall into one of two categories: A spindle with a male taper and the chuck having a female taper; or a spindle with a female taper, a chuck with a female taper and an adapter with a male taper on each end that goes between the chuck and spindle. Each style has their place, with the adaptor style being used more on the bigger Presses.
Alright, there’s your ‘taper background’, now let’s get specific. Drill Press tapers engage (‘seat’) best with a shock. I know some manufacturers who tell you to just push them together, but that’s not the best way. Let’s say that you have a Drill Press with a female tapered chuck and the spindle has the male taper sticking down. First, clean the tapers completely to remove any oil, grease or coating that could prevent metal on metal contact. My favorite solution to this is an old rag saturated with acetone (NOTE: if you use acetone, be aware that it is highly combustible). Next, once the tapers are cleaned, turn the chuck so as to retract the chuck jaws. Next, Place the chuck onto the spindle taper by hand. Finally comes the ‘shock’ part. Put a small 2X4 underneath the chuck jaw opening and use a small mallet (I have a 3lb sledge for this) to hit upward on the 2X4 (chuck bottom). One good sharp whack ought to do it.
Once the tapers are seated properly, they will usually remain engaged unless something too large or out of balance is put into the chuck.
#23 - The Story of Mrs. Mayberry - Part 4
Picking up where we left off, with Mrs. Mayberry back on the road and us thoroughly enjoying her…We’ve won a “people’s choice” award, a second in class at an antique auto show and had her in a Christmas parade in Millington, TN…and the adventure is just beginning.
Since the time I originally wrote this story, we put another 6000 miles on Mrs. Mayberry and even drove her all the way to Branson, MO for a show. Unfortunately in 2005, time, and not being used for those 10 years, took its toll and the motor lost its compression. We just couldn’t get her cranked again. It wasn’t unexpected because getting 60,000 miles out of a car back in 1955 was doing pretty good, even for one that was maintained perfectly. It was still kind of sad, tho.
Due to a job change and relocating to Murfreesboro from Jackson, I wasn’t able to get to work on the motor until 2008. But work on her, we did. I had Mike’s Speed Shop do the machine work (by the way- those guys are great!) We bored her out, put hardened valve seats in and a new camshaft. I even found a decent ‘how-to’ book about the Ford Y-blocks and put a couple of tricks into the motor to keep her lubricated far better than she was out of the Ford factory.
Anyway, we got her going again and have been going to shows and cruise-ins for over 2 years now and but for a leaky top radiator hose, she has been just fine. We even drove her back to Mt. Airy to visit the daughter of the original owner- that was a 7 hour, 410 mile trip –one way. I must say that big old 281 (it was a 272 but we bored it out, remember?) just rolled on down the highway. She wasn’t designed for interstates because there weren’t any back in 1955, so we cruise down the State roads whenever possible and practical.
We do hang out at the Auto Garage in Cannonsburgh a lot and it’s quite possible that you might see us out on the roads when the weather is good. We even had occasion to display her at our church (World Outreach) last father’s day and it was really a hoot talking to the folks about her. There was one particular lady about my age (maybe a few years older) who said she had learned to drive on a ’55 Ford. She stopped by before service, and then was back again after service, so, me being me, I told her “If you can remember the trick to starting it, here’s the keys, take her for a spin.” She looked flabbergasted…and then you could see the wheels in her mind turning…trying to remember what the ‘trick’ is.
She didn’t recall it, but I love connecting with people’s fond memories of their past - that’s what it’s all about.
Since the time I originally wrote this story, we put another 6000 miles on Mrs. Mayberry and even drove her all the way to Branson, MO for a show. Unfortunately in 2005, time, and not being used for those 10 years, took its toll and the motor lost its compression. We just couldn’t get her cranked again. It wasn’t unexpected because getting 60,000 miles out of a car back in 1955 was doing pretty good, even for one that was maintained perfectly. It was still kind of sad, tho.
Due to a job change and relocating to Murfreesboro from Jackson, I wasn’t able to get to work on the motor until 2008. But work on her, we did. I had Mike’s Speed Shop do the machine work (by the way- those guys are great!) We bored her out, put hardened valve seats in and a new camshaft. I even found a decent ‘how-to’ book about the Ford Y-blocks and put a couple of tricks into the motor to keep her lubricated far better than she was out of the Ford factory.
Anyway, we got her going again and have been going to shows and cruise-ins for over 2 years now and but for a leaky top radiator hose, she has been just fine. We even drove her back to Mt. Airy to visit the daughter of the original owner- that was a 7 hour, 410 mile trip –one way. I must say that big old 281 (it was a 272 but we bored it out, remember?) just rolled on down the highway. She wasn’t designed for interstates because there weren’t any back in 1955, so we cruise down the State roads whenever possible and practical.
We do hang out at the Auto Garage in Cannonsburgh a lot and it’s quite possible that you might see us out on the roads when the weather is good. We even had occasion to display her at our church (World Outreach) last father’s day and it was really a hoot talking to the folks about her. There was one particular lady about my age (maybe a few years older) who said she had learned to drive on a ’55 Ford. She stopped by before service, and then was back again after service, so, me being me, I told her “If you can remember the trick to starting it, here’s the keys, take her for a spin.” She looked flabbergasted…and then you could see the wheels in her mind turning…trying to remember what the ‘trick’ is.
She didn’t recall it, but I love connecting with people’s fond memories of their past - that’s what it’s all about.
Friday, July 9, 2010
#22 - The Story of Mrs. Mayberry - Part 3
Picking up where we left off, with us going back to Mt. Airy and trying to get Ms. Mayberry on the trailer for the trip home, and finding a dead battery… Even though I was never a Boy Scout, I have always believed in being prepared so I went to my truck and took a 6 volt battery out of the back. I had used this battery in my 1934 Ford, but had recently changed that car to a 12 volt system, so this battery was sitting there waiting to be used elsewhere. Little did I know that it would be in a 1955 Ford Fairlane. When Mr. Mittman saw me take the battery out, he said, “Wow, you really did come ready for anything.” We put my 6 volt battery in Mrs. Mayberry, cranked her up, loaded her up, and headed for home.
The trip home was uneventful and once we got back, I put the car in the air and proceeded to give her a good once over. The brake cylinders were corroded, the exhaust pipes were rotted and the master cylinder leaked. Even the heater core was leaking onto the carpet. I replaced all the brake components (hoses, shoes, cylinders, etc) and bypassed the heater. It still ran kind of rough on take off, but I thought a good tune-up was in order. To my surprise, I took her down to get new exhaust pipes, and mufflers, installed and once those were in, she ran like a new car. The old mufflers had corroded and collapsed internally.
But Mrs. Mayberry was on the road…July of 2003.
We put about 1000 miles on her and only had one real scare. On the way back home from a cruise in Union City, TN, she started running horribly, almost like on 2 cylinders. I thought we had broken a rocker arm or something internal in the engine. As we limped along, I decided to try the choke to see if the carburetor was plugged. Lo and behold, she perked right up and we made it back home fine. After getting home, I decided to rebuild the carburetor and in my “junk box” I found a carburetor that my dad had used on one of his dirt track stock cars back in the late 1950’s. It was exactly the right carb for Mrs. Mayberry, so I rebuilt it and put it in. Boy, did that wake that big 272 cubic inch motor up! After a while I had to put in smaller carburetor jets, but that’s not surprising…Ms. Mayberry isn’t a race car. She is just a sweet old car that has found herself a new home with folks who appreciate her and who will enjoy making new family memories with her.
Next week - part 4.
The trip home was uneventful and once we got back, I put the car in the air and proceeded to give her a good once over. The brake cylinders were corroded, the exhaust pipes were rotted and the master cylinder leaked. Even the heater core was leaking onto the carpet. I replaced all the brake components (hoses, shoes, cylinders, etc) and bypassed the heater. It still ran kind of rough on take off, but I thought a good tune-up was in order. To my surprise, I took her down to get new exhaust pipes, and mufflers, installed and once those were in, she ran like a new car. The old mufflers had corroded and collapsed internally.
But Mrs. Mayberry was on the road…July of 2003.
We put about 1000 miles on her and only had one real scare. On the way back home from a cruise in Union City, TN, she started running horribly, almost like on 2 cylinders. I thought we had broken a rocker arm or something internal in the engine. As we limped along, I decided to try the choke to see if the carburetor was plugged. Lo and behold, she perked right up and we made it back home fine. After getting home, I decided to rebuild the carburetor and in my “junk box” I found a carburetor that my dad had used on one of his dirt track stock cars back in the late 1950’s. It was exactly the right carb for Mrs. Mayberry, so I rebuilt it and put it in. Boy, did that wake that big 272 cubic inch motor up! After a while I had to put in smaller carburetor jets, but that’s not surprising…Ms. Mayberry isn’t a race car. She is just a sweet old car that has found herself a new home with folks who appreciate her and who will enjoy making new family memories with her.
Next week - part 4.
Thursday, July 8, 2010
#21 - The Story of Ms. Mayberry - Part 2
Picking up where we left off, with Ms. Mayberry (a one-owner, 1955 Ford Fairlane, Town Sedan) getting banished to a garage for 10 years….Unfortunately, this was the same garage that she used for sheltering her cats. Sometime around 2001, Mr. Mittman bought the car from Mr. Harris’s daughter and took it down to his shop. Once there, the damage from the cat urine was evident. Some parts of the lower body and the chrome bumpers and guards needed attention. The most fortunate part of it was that the car’s windows were always up, so no cat ever got inside.
Mr. Mittman had the bumpers and accessory bumper guards re-chromed and the gas tank boiled out and ‘re-nued’ (which is an operation to coat the inside of the tank with epoxy). He had the front door upholstery redone because of wear around the door handles and did the bodywork necessary to be able to repaint the car in its original colors: Sea Sprite Green and Snowshoe White. Once he had the car looking good, he parked it alongside his shop and waited for the right folks to come by.
It looks like my wife and I were “the right folks” because after talking to Mr. Mittman, and hearing what his price for the car was, we decided to go back and take a closer look…and this time, we’d take the car trailer with us.
The third weekend of June, we made a flying trip back to Mt. Airy to seriously check the car out. When we drove up to Mr. Mittman’s shop the car was sitting there running and I had to look twice at the turning fan blade to make sure…it was smooth. We got in it to take a test drive and started off down the street. At the first traffic light, I stepped on the brakes and the right front tire locked into a skid. That squealing tire sure made lots of folks sit up and take notice. Then, after taking off again, she stumbled a bit, like she might need a tune-up. We drove over to Ms. Starr’s house (the daughter of the original owner) and the brakes wouldn’t stop the car. Luckily, the parking brake worked ok, so we made it up her driveway just fine.
Ms. Starr came out and talked with us and told us of how many fond memories she had of being in the car with her folks. She even made the comment that my wife reminded her of her own mother getting out of the car. After a while, we decided we needed to get on the road, so we headed back to Mr. Mittman’s shop, to finalize the deal. Once we had completed the paperwork, we went outside to crank the car and put it on the trailer for the trip back to Jackson, TN…and the battery was dead.
Next week- part 3.
Mr. Mittman had the bumpers and accessory bumper guards re-chromed and the gas tank boiled out and ‘re-nued’ (which is an operation to coat the inside of the tank with epoxy). He had the front door upholstery redone because of wear around the door handles and did the bodywork necessary to be able to repaint the car in its original colors: Sea Sprite Green and Snowshoe White. Once he had the car looking good, he parked it alongside his shop and waited for the right folks to come by.
It looks like my wife and I were “the right folks” because after talking to Mr. Mittman, and hearing what his price for the car was, we decided to go back and take a closer look…and this time, we’d take the car trailer with us.
The third weekend of June, we made a flying trip back to Mt. Airy to seriously check the car out. When we drove up to Mr. Mittman’s shop the car was sitting there running and I had to look twice at the turning fan blade to make sure…it was smooth. We got in it to take a test drive and started off down the street. At the first traffic light, I stepped on the brakes and the right front tire locked into a skid. That squealing tire sure made lots of folks sit up and take notice. Then, after taking off again, she stumbled a bit, like she might need a tune-up. We drove over to Ms. Starr’s house (the daughter of the original owner) and the brakes wouldn’t stop the car. Luckily, the parking brake worked ok, so we made it up her driveway just fine.
Ms. Starr came out and talked with us and told us of how many fond memories she had of being in the car with her folks. She even made the comment that my wife reminded her of her own mother getting out of the car. After a while, we decided we needed to get on the road, so we headed back to Mr. Mittman’s shop, to finalize the deal. Once we had completed the paperwork, we went outside to crank the car and put it on the trailer for the trip back to Jackson, TN…and the battery was dead.
Next week- part 3.
Thursday, June 24, 2010
#20 - The Story of Ms. Mayberry - Part 1
I decided it was time for another ‘detour’ this week. Tools are kool, but there are other things going on that you might want to read about.
On the 5th of June, 2003, my wife and I were on our honeymoon. We were cruising the backloads of Virginia and North Carolina, and we decided to visit Mt. Airy, NC…the real “Mayberry”…Andy Griffith’s hometown.
We toured the local museum and the “Mayberry” jail, and even had our picture taken with “Floyd the barber”. He was a cool old fellow and the wall in his shop – yes, he really is a barber – is just covered with pictures of people and celebrities who have been in there.
We started out of Mt. Airy, attempting to take route 601 South but unknowingly, I turned a block too early. As we headed down a hill toward an intersection, we passed an Auto Body Shop and noticed a long row of cars sitting facing the road. Among the cars was a really pretty 1955 Ford. It caught our attention, so we turned around and drove back to take a look. There was no “for sale” sign, but this Ford was looking real good. It had an unusual paint pattern on because the color was above the white. We had never seen that before. The chrome was nice, the paint did look sharp and the interior looked like it had just rolled out of the factory. We could tell that it was an original interior because of the small cigarette burns that occur when a smoking driver doesn’t quite get the cigarette out of the vent window and instead burns the upholstery. We checked it out for a bit and then got back in the truck and headed on our way.
Once home and back into the daily routine (if that’s even an accurate statement for newlyweds), I couldn’t get that ’55 off my mind. So, I called back to Mt. Airy and after a few days of talking to the Chamber of Commerce and several other area people, I was able to find out that Mr. John Mittman owned the Body Shop, and presumably the ’55.
After a few tries, I was able to talk to Mr. Mittman, who relayed to story of “Ms. Mayberry” (our new name for the ’55) to me.
A fellow named Mr. Watson Harris had bought his car new, in 1955. Mr. Harris only drove it to church and to Florida once or twice over the 46 years that he used it. The car had only 56,300 miles on it when Mr. Harris passed away in 1991. Mr. Harris’s daughter put the ’55 into a one-car garage and left it there for the next 10years.
Next week- part 2.
Send your questions or comments to:
Toolsmartz@bellsouth.net and we’ll see what we can do to help you.
On the 5th of June, 2003, my wife and I were on our honeymoon. We were cruising the backloads of Virginia and North Carolina, and we decided to visit Mt. Airy, NC…the real “Mayberry”…Andy Griffith’s hometown.
We toured the local museum and the “Mayberry” jail, and even had our picture taken with “Floyd the barber”. He was a cool old fellow and the wall in his shop – yes, he really is a barber – is just covered with pictures of people and celebrities who have been in there.
We started out of Mt. Airy, attempting to take route 601 South but unknowingly, I turned a block too early. As we headed down a hill toward an intersection, we passed an Auto Body Shop and noticed a long row of cars sitting facing the road. Among the cars was a really pretty 1955 Ford. It caught our attention, so we turned around and drove back to take a look. There was no “for sale” sign, but this Ford was looking real good. It had an unusual paint pattern on because the color was above the white. We had never seen that before. The chrome was nice, the paint did look sharp and the interior looked like it had just rolled out of the factory. We could tell that it was an original interior because of the small cigarette burns that occur when a smoking driver doesn’t quite get the cigarette out of the vent window and instead burns the upholstery. We checked it out for a bit and then got back in the truck and headed on our way.
Once home and back into the daily routine (if that’s even an accurate statement for newlyweds), I couldn’t get that ’55 off my mind. So, I called back to Mt. Airy and after a few days of talking to the Chamber of Commerce and several other area people, I was able to find out that Mr. John Mittman owned the Body Shop, and presumably the ’55.
After a few tries, I was able to talk to Mr. Mittman, who relayed to story of “Ms. Mayberry” (our new name for the ’55) to me.
A fellow named Mr. Watson Harris had bought his car new, in 1955. Mr. Harris only drove it to church and to Florida once or twice over the 46 years that he used it. The car had only 56,300 miles on it when Mr. Harris passed away in 1991. Mr. Harris’s daughter put the ’55 into a one-car garage and left it there for the next 10years.
Next week- part 2.
Send your questions or comments to:
Toolsmartz@bellsouth.net and we’ll see what we can do to help you.
Thursday, June 3, 2010
#19 - Setting your bandsaw blade to track properly.
Let’s talk a little more about the bandsaw this week.
Bandsaws can do things that table saws can only dream of, which makes them pretty much a necessity in a shop; however, they need to be set up properly and to do that one needs to keep a few things in mind.
Just to start with a proper definition, bandsaw “wheels” are the spoked or solid items/wheels that are mounted on the axles. Bandsaw “tires” are the rubber, or urethane, coatings on the rim of the wheels, that the blade actually rides on. Typically, the tires can be removed from the wheels.
Most good bandsaws use a wheel/tire combination that is ‘crowned’. In other words, where the blade rides, the surface has a distinct ‘hump’ in it. This hump/crown allows the blade to be tracked (def: - centered on the tire) with much more precision than if the tire/wheel were simply flat. On the Delta 14” bandsaws that I am most familiar with, the wheel itself had the crown machined into it and the rubber tire was just flat rubber. When the tire was installed, it conformed to the crown of the wheel.
There are some ‘bandsaw guys’ that say the crown gives the operator the ability to adjust the blade to compensate for blade drift (our last week’s discussion), but in over 25 years, I never saw that as a workable option.
Setting up the blade tracking is not really a difficult thing, but like most adjustable items, one can wind up chasing their tail if they aren’t careful.
Tracking the blade first requires that you center the blade on the bottom tire and the top tire. Once you have the blade centered, blade tension should be applied. I like to start out with only ½ to ¾ of full tension, until the tracking gets fully set. Ok, the blade is on, the tension is set at ½ and the blade is centered on the tires. At this point, roll the wheels and see if the blade stays centered on the tires. If it does, go ahead and apply full tension and roll the wheels again. If the blade stays on and centered, you are probably good to go.
If your initial testing shows the blade trying to creep towards the edge of the wheel, you will need to use the saw’s tracking adjustment to coax the blade back towards the center of the tire. When the blade stays close to the center of the tires, the saw should do its job just fine.
Send your questions or comments to:
Toolsmartz@bellsouth.net and we’ll see what we can do to help you.
_______________________________________________________________
Any views or opinions presented in this article are solely those of the author and do not necessarily represent those of this newspaper. Neither the author, nor this newspaper, accepts any liability for the content of this article, or for the consequences of any actions taken on the basis of the information provided.
Bandsaws can do things that table saws can only dream of, which makes them pretty much a necessity in a shop; however, they need to be set up properly and to do that one needs to keep a few things in mind.
Just to start with a proper definition, bandsaw “wheels” are the spoked or solid items/wheels that are mounted on the axles. Bandsaw “tires” are the rubber, or urethane, coatings on the rim of the wheels, that the blade actually rides on. Typically, the tires can be removed from the wheels.
Most good bandsaws use a wheel/tire combination that is ‘crowned’. In other words, where the blade rides, the surface has a distinct ‘hump’ in it. This hump/crown allows the blade to be tracked (def: - centered on the tire) with much more precision than if the tire/wheel were simply flat. On the Delta 14” bandsaws that I am most familiar with, the wheel itself had the crown machined into it and the rubber tire was just flat rubber. When the tire was installed, it conformed to the crown of the wheel.
There are some ‘bandsaw guys’ that say the crown gives the operator the ability to adjust the blade to compensate for blade drift (our last week’s discussion), but in over 25 years, I never saw that as a workable option.
Setting up the blade tracking is not really a difficult thing, but like most adjustable items, one can wind up chasing their tail if they aren’t careful.
Tracking the blade first requires that you center the blade on the bottom tire and the top tire. Once you have the blade centered, blade tension should be applied. I like to start out with only ½ to ¾ of full tension, until the tracking gets fully set. Ok, the blade is on, the tension is set at ½ and the blade is centered on the tires. At this point, roll the wheels and see if the blade stays centered on the tires. If it does, go ahead and apply full tension and roll the wheels again. If the blade stays on and centered, you are probably good to go.
If your initial testing shows the blade trying to creep towards the edge of the wheel, you will need to use the saw’s tracking adjustment to coax the blade back towards the center of the tire. When the blade stays close to the center of the tires, the saw should do its job just fine.
Send your questions or comments to:
Toolsmartz@bellsouth.net and we’ll see what we can do to help you.
_______________________________________________________________
Any views or opinions presented in this article are solely those of the author and do not necessarily represent those of this newspaper. Neither the author, nor this newspaper, accepts any liability for the content of this article, or for the consequences of any actions taken on the basis of the information provided.
#18 - Making your bandsaw give a straight cut.
We finally got to go see the movie, “Letters to God” and I must say that living that life episode must have been incredibly difficult for everyone who loved Tyler. Go see the movie; it’s a good ‘un.
Let’s go back and visit our old friend the bandsaw, this week. One of the most common problems with a bandsaw is getting it to cut straight. You start out with a nice straight line and start the cut and before you know it, the blade has decided that it wants to shoot off at an angle and destroy the part you did not want cut. Some of the ‘old pros’ call this ‘blade drift’- I call it ‘don’t cut straight’.
Most often, here is what happens. Looking directly at the blade teeth, one notices that each tooth on the blade is bent out at a precise distance. This is called the ‘set’ of the blade. Having the teeth set outward provides clearance for the back of the blade to move through the work. It also provides some clearance for the blade to cut around a curve. However, if (for example) the teeth that are bent to the right stick out further than the teeth that are bent to the left, the blade will cut towards the right. The best solution to this problem is to purchase a high-quality blade, but I have even seen those drift sideways - right out of the box.
Another solution is to make the ‘set’ more equal - more balanced, if you will.
One way to do that would be to increase the bend of the teeth that are not sticking out as far; however, that is a very difficult thing to do. The more practical solution would be to slightly file the tips of the teeth that are sticking out too far- actually you would be ‘dulling’ them ever so little.
A method I have used is to hold a whetstone against the running blade and let the blade teeth lightly skim across the surface of the stone. A fine touch is a must, but with some practice, it isn’t hard to manage. Take your time and test the blade often by taking a test cut, so that you don’t dull them down too far.
Another thing that causes blade drift is when the number of blade teeth per inch is too high and the wood chips cannot escape from in between them. This typically shows up when doing resawing – sawing very thick wood – because the blade spends a lot of time inside the wood and can actually heat up and bow inside the wood, thereby causing a warped cut. The solution is simple: Use a blade with fewer teeth per inch.
Send your questions or comments to:
Toolsmartz@bellsouth.net and we’ll see what we can do to help you.
_______________________________________________________________
Any views or opinions presented in this article are solely those of the author and do not necessarily represent those of this newspaper. Neither the author, nor this newspaper, accepts any liability for the content of this article, or for the consequences of any actions taken on the basis of the information provided.
Let’s go back and visit our old friend the bandsaw, this week. One of the most common problems with a bandsaw is getting it to cut straight. You start out with a nice straight line and start the cut and before you know it, the blade has decided that it wants to shoot off at an angle and destroy the part you did not want cut. Some of the ‘old pros’ call this ‘blade drift’- I call it ‘don’t cut straight’.
Most often, here is what happens. Looking directly at the blade teeth, one notices that each tooth on the blade is bent out at a precise distance. This is called the ‘set’ of the blade. Having the teeth set outward provides clearance for the back of the blade to move through the work. It also provides some clearance for the blade to cut around a curve. However, if (for example) the teeth that are bent to the right stick out further than the teeth that are bent to the left, the blade will cut towards the right. The best solution to this problem is to purchase a high-quality blade, but I have even seen those drift sideways - right out of the box.
Another solution is to make the ‘set’ more equal - more balanced, if you will.
One way to do that would be to increase the bend of the teeth that are not sticking out as far; however, that is a very difficult thing to do. The more practical solution would be to slightly file the tips of the teeth that are sticking out too far- actually you would be ‘dulling’ them ever so little.
A method I have used is to hold a whetstone against the running blade and let the blade teeth lightly skim across the surface of the stone. A fine touch is a must, but with some practice, it isn’t hard to manage. Take your time and test the blade often by taking a test cut, so that you don’t dull them down too far.
Another thing that causes blade drift is when the number of blade teeth per inch is too high and the wood chips cannot escape from in between them. This typically shows up when doing resawing – sawing very thick wood – because the blade spends a lot of time inside the wood and can actually heat up and bow inside the wood, thereby causing a warped cut. The solution is simple: Use a blade with fewer teeth per inch.
Send your questions or comments to:
Toolsmartz@bellsouth.net and we’ll see what we can do to help you.
_______________________________________________________________
Any views or opinions presented in this article are solely those of the author and do not necessarily represent those of this newspaper. Neither the author, nor this newspaper, accepts any liability for the content of this article, or for the consequences of any actions taken on the basis of the information provided.
Saturday, May 22, 2010
#17 - What to do with flood-drenched machines - Part 2
As we talked about last issue, we’re trying to help those folks who need to get their machines running again…but not just ‘get them running’ but KEEP them running, with minimal damage.
If you have someone whose machines have been submerged in the flood water, please let them know about this week’s column and if they need to see Part 1 (last week’s column) send me an email and I will forward them a copy. Also, about a month ago, I answered a question about rusty table tops - anyone who is interested in checking that column out, drop me an email and I will send it out.
Alright, back to business. We were discussing motors and had stopped before we stepped off the cliff and brought up those small brush motors, also known as ‘Universal’ motors. These are your miter saw motors, benchtop planer motors and even your battery tool motors. The design as been time-tested and proven to be a good choice in small tools, but when those tools find themselves under flood water, there is a real choice to make.
Given what we talked about last week- the extremely abrasive nature of flood water- the choices are limited to spending a good amount of time taking the motor apart and cleaning/drying it out, or just replacing the motor. Only you can make that choice, but if you decide to clean/dry it, here are a few things you need to consider. Your motor bearings and all associated bearings need replacing. The commutator/brush mating surface needs to be cleaned with a commutator stone. All of the internal gear grease associated with the motor will need changing. At this point, depending on the size of the affected motor, it might cost less to replace the motor. Obviously, all of them CAN be cleaned, but on the smaller motors/tools…I’d opt for getting a new one.
OK, let’s talk about bearings. A good rule of thumb is: if the bearings are sealed and they were only under water for less than 15 minutes, and they were immediately washed and dried, they might be OK…ALL other bearings need to be replaced. Remember our discussion about the microscopic grit that permeates flood water? I can’t think of anything that will eat up your bearings faster. Just be safe, rather than sorry, and replace all of them.
Hopefully, these two columns have been useful to some of you. If you have any questions or comments please send me an email at:
Toolsmartz@bellsouth.net and we’ll see what we can do to help you.
_______________________________________________________________
Any views or opinions presented in this article are solely those of the author and do not necessarily represent those of this newspaper. Neither the author, nor this newspaper, accepts any liability for the content of this article, or for the consequences of any actions taken on the basis of the information provided.
If you have someone whose machines have been submerged in the flood water, please let them know about this week’s column and if they need to see Part 1 (last week’s column) send me an email and I will forward them a copy. Also, about a month ago, I answered a question about rusty table tops - anyone who is interested in checking that column out, drop me an email and I will send it out.
Alright, back to business. We were discussing motors and had stopped before we stepped off the cliff and brought up those small brush motors, also known as ‘Universal’ motors. These are your miter saw motors, benchtop planer motors and even your battery tool motors. The design as been time-tested and proven to be a good choice in small tools, but when those tools find themselves under flood water, there is a real choice to make.
Given what we talked about last week- the extremely abrasive nature of flood water- the choices are limited to spending a good amount of time taking the motor apart and cleaning/drying it out, or just replacing the motor. Only you can make that choice, but if you decide to clean/dry it, here are a few things you need to consider. Your motor bearings and all associated bearings need replacing. The commutator/brush mating surface needs to be cleaned with a commutator stone. All of the internal gear grease associated with the motor will need changing. At this point, depending on the size of the affected motor, it might cost less to replace the motor. Obviously, all of them CAN be cleaned, but on the smaller motors/tools…I’d opt for getting a new one.
OK, let’s talk about bearings. A good rule of thumb is: if the bearings are sealed and they were only under water for less than 15 minutes, and they were immediately washed and dried, they might be OK…ALL other bearings need to be replaced. Remember our discussion about the microscopic grit that permeates flood water? I can’t think of anything that will eat up your bearings faster. Just be safe, rather than sorry, and replace all of them.
Hopefully, these two columns have been useful to some of you. If you have any questions or comments please send me an email at:
Toolsmartz@bellsouth.net and we’ll see what we can do to help you.
_______________________________________________________________
Any views or opinions presented in this article are solely those of the author and do not necessarily represent those of this newspaper. Neither the author, nor this newspaper, accepts any liability for the content of this article, or for the consequences of any actions taken on the basis of the information provided.
Saturday, May 15, 2010
#16 - What to do with flood-drenched machines - Part 1
We’ve had many areas under water from the flooding last weekend and I was thinking that there might be some folks who had their machines get drowned. So, I decided to pull in some resources to help me put out some practical information that some might find useful in this situation. My main resource for this column is my friend Bob Vaughan from Roanoke, VA. Bob and I go way back to my days at Delta Tech Service and he has been on the frontlines ‘fighting the good fight’ of keeping machines alive for longer than he’d care to admit, I’m sure.
If you have someone whose machines have been submerged in the flood water, please let them know about the next two columns- maybe they could use the advice.
First off, what we do NOT want to do is wash the machines off and just let them dry. Here’s why: Flood water carries silt which is fine, microscopic rock. These little rocks are very abrasive. In fact, it would not surprise me if sandpaper was made from silt rock. Point being, anything exposed to the water will have a fine coating of this abrasive on it. The flood water abrasive needs to be cleaned off of ALL working surfaces and shafts that are prone to friction. For instance, table saw trunnions, driven and drive gears, dovetail ways, ANY mating surfaces that move on each other must all be cleaned - not just dried.
The machine’s motor starter would need to be disassembled, wiped out and have its internal contact tips cleaned. If you only have a toggle style switch, I would suggest replacing it, unless it happens to be the kind of toggle switch that you can take apart and thoroughly clean.
The motor itself needs particular attention. The easiest motor to revive would be a 3-phase motor because it has no brushes or centrifugal switch to be concerned about. If you have a 3-phase motor, take it apart, wash it completely, change the bearings and let it dry a few days - preferably in a dehumidified environment. Reassemble it and it should be fine.
For a standard 1 phase motor, take it apart (including the capacitor housings if it has them), wash it completely, replace the bearings, clean the centrifugal switch and its contact tips and let it dry a few days (again, in the dehumidified environment). Once it is dry, put it back together and it should be good to go.
Next week we’ll talk about those little universal (brush) motors and your bearings.
Send your questions or comments to:
Toolsmartz@bellsouth.net and we’ll see what we can do to help you.
_______________________________________________________________
Any views or opinions presented in this article are solely those of the author and do not necessarily represent those of this newspaper. Neither the author, nor this newspaper, accepts any liability for the content of this article, or for the consequences of any actions taken on the basis of the information provided.
If you have someone whose machines have been submerged in the flood water, please let them know about the next two columns- maybe they could use the advice.
First off, what we do NOT want to do is wash the machines off and just let them dry. Here’s why: Flood water carries silt which is fine, microscopic rock. These little rocks are very abrasive. In fact, it would not surprise me if sandpaper was made from silt rock. Point being, anything exposed to the water will have a fine coating of this abrasive on it. The flood water abrasive needs to be cleaned off of ALL working surfaces and shafts that are prone to friction. For instance, table saw trunnions, driven and drive gears, dovetail ways, ANY mating surfaces that move on each other must all be cleaned - not just dried.
The machine’s motor starter would need to be disassembled, wiped out and have its internal contact tips cleaned. If you only have a toggle style switch, I would suggest replacing it, unless it happens to be the kind of toggle switch that you can take apart and thoroughly clean.
The motor itself needs particular attention. The easiest motor to revive would be a 3-phase motor because it has no brushes or centrifugal switch to be concerned about. If you have a 3-phase motor, take it apart, wash it completely, change the bearings and let it dry a few days - preferably in a dehumidified environment. Reassemble it and it should be fine.
For a standard 1 phase motor, take it apart (including the capacitor housings if it has them), wash it completely, replace the bearings, clean the centrifugal switch and its contact tips and let it dry a few days (again, in the dehumidified environment). Once it is dry, put it back together and it should be good to go.
Next week we’ll talk about those little universal (brush) motors and your bearings.
Send your questions or comments to:
Toolsmartz@bellsouth.net and we’ll see what we can do to help you.
_______________________________________________________________
Any views or opinions presented in this article are solely those of the author and do not necessarily represent those of this newspaper. Neither the author, nor this newspaper, accepts any liability for the content of this article, or for the consequences of any actions taken on the basis of the information provided.
Friday, May 7, 2010
#15 - Proper Saw Blade Alignment is a must.
Ok, let’s see if, after a couple of trips to never-never land, we can get back on track this week.
Let’s talk table saws.
One of the most common adjustments on table saws is that of making sure the blade is properly aligned within the saw. There are several indicators that let one know that the blade is not in proper alignment. The operator could see some burning on the side of the stock. There could be some excessive roughness on the sides of the cut. There might be a tendency for the stock to lift at the back of the cut or even kickback at the operator. This isn’t a complete list, just those that are the most common.
When those conditions are showing up in your work, it’s time to do a bit of blade alignment checking. It’s not difficult when done the right way.
First, choose an accurate ruler with which to measure. Personally, for this task, I use a combination square because it can be locked to a length and you can hang it inside the miter slot. Raise the blade to maximum height and pick one blade tooth and mark it. Rotate the blade so as to put the chosen tooth at the front of the saw. Measure the distance from that tooth to the miter slot in the table and write it down. (This is where the combination square comes in handy- it can be locked into that distance and you know it stays accurate) Then rotate the blade backwards which puts the chosen tooth at the rear of the saw. Measure the distance from that tooth to the miter slot. These two measurements must be the same.
The reason for using one particular tooth is to eliminate any possibility of the blade being warped and that causing your measurement to be inaccurate.
Once it has been determined that the measurements are not the same, it’s time to get the blade properly aligned. In my experience all table saws, no matter their size, have the means to align the blade to the miter slot. What needs to be done is to determine exactly how this is accomplished on the particular saw that is being checked. Start by looking at the undercarriage of the saw and see how the saw arbor is hanging from the table. That should tell you where you need to loosen to be able to shift the saw arbor to properly align the blade. Most Contractor-style saws have 4 bolts that hang the undercarriage to the bottom of the table. Most larger saws have an independent table and the undercarriage hangs from the cabinet. On those saws, simply loosening the table to cabinet bolts allow for the alignment adjustment.
Send your questions or comments to:
Toolsmartz@bellsouth.net and we’ll see what we can do to help you.
_______________________________________________________________
Any views or opinions presented in this article are solely those of the author and do not necessarily represent those of this newspaper. Neither the author, nor this newspaper, accepts any liability for the content of this article, or for the consequences of any actions taken on the basis of the information provided.
Let’s talk table saws.
One of the most common adjustments on table saws is that of making sure the blade is properly aligned within the saw. There are several indicators that let one know that the blade is not in proper alignment. The operator could see some burning on the side of the stock. There could be some excessive roughness on the sides of the cut. There might be a tendency for the stock to lift at the back of the cut or even kickback at the operator. This isn’t a complete list, just those that are the most common.
When those conditions are showing up in your work, it’s time to do a bit of blade alignment checking. It’s not difficult when done the right way.
First, choose an accurate ruler with which to measure. Personally, for this task, I use a combination square because it can be locked to a length and you can hang it inside the miter slot. Raise the blade to maximum height and pick one blade tooth and mark it. Rotate the blade so as to put the chosen tooth at the front of the saw. Measure the distance from that tooth to the miter slot in the table and write it down. (This is where the combination square comes in handy- it can be locked into that distance and you know it stays accurate) Then rotate the blade backwards which puts the chosen tooth at the rear of the saw. Measure the distance from that tooth to the miter slot. These two measurements must be the same.
The reason for using one particular tooth is to eliminate any possibility of the blade being warped and that causing your measurement to be inaccurate.
Once it has been determined that the measurements are not the same, it’s time to get the blade properly aligned. In my experience all table saws, no matter their size, have the means to align the blade to the miter slot. What needs to be done is to determine exactly how this is accomplished on the particular saw that is being checked. Start by looking at the undercarriage of the saw and see how the saw arbor is hanging from the table. That should tell you where you need to loosen to be able to shift the saw arbor to properly align the blade. Most Contractor-style saws have 4 bolts that hang the undercarriage to the bottom of the table. Most larger saws have an independent table and the undercarriage hangs from the cabinet. On those saws, simply loosening the table to cabinet bolts allow for the alignment adjustment.
Send your questions or comments to:
Toolsmartz@bellsouth.net and we’ll see what we can do to help you.
_______________________________________________________________
Any views or opinions presented in this article are solely those of the author and do not necessarily represent those of this newspaper. Neither the author, nor this newspaper, accepts any liability for the content of this article, or for the consequences of any actions taken on the basis of the information provided.
Wednesday, May 5, 2010
#14 - The Story of Thunder Road
Well, due to a ‘special request’, we taking another ‘detour’ this week. This a story about my first car, and yes, I do still have it.
We lived in Memphis, TN and my dad was a truck driver. One Friday night in 1972, he came home and told my mom that they had to make a road trip the next day. He wouldn’t tell me why. They got up early on Saturday and late that afternoon, they came back, with my mom driving our ‘normal’ car and dad was driving…well...what was that? It turned out to be a 1950 Ford Crestliner that he found in Gordo, AL. His first words about it were- “You need to fix the brakes”.
The drivetrain had been replaced with 1964 Falcon Sprint components – a 260ci V8, a four speed trans and an 8 inch rear. The vinyl top had been sprayed on and the original Coronation Red metallic had some funky green painted over it…but it was MINE!
Over the next few months I learned to arc weld because I had to constantly change out the exhaust system. I’d go thru city inspection with a normal muffler and get home and swap it out for a Thrush glasspack.
The speedometer didn’t work, so there is no telling how many miles I racked up on that car over the next 6-7 years. I joined the Navy in ’73 and took the car to Virginia and back, several times. Then we transferred to Florida and drove it down there…breaking the rearend gear when we hit the state line.
We went thru 5 different paint jobs over the next 33 years, one engine overhaul, a fresh rearend and many, many gallons of gas. In 1980, I swapped in a 1965, 396ci Chevy motor with a powerglide. While the ‘Ford guy’ in me wanted to keep it all Ford, that 396 dropped in so sweetly that it would have been a crime not to put it in.
When I remarried in 2003, I still had my Crestliner- still in primer, didn’t run, no interior…a true ‘project car’. My new, lovely wife, decided she had seen enough of the primer and she wanted to go cruising, so we had the car done right by The Hot Rod Shop in Corinth, MS. The 50’s parts list reads like a who’s who of automotive goodies: 1965 Chevy 396, 700r4 trans, Fatman spindles, power windows, killer stereo system, front disc brakes, 2003 Mustang Laser Red and ’73 GMC Sliver paint, 2003 Chrysler Sebring convertible front seats and whitewall radials.
This is our cruiser and there is no telling where we might show up…not too bad for a 60 year old car that I have owned for 38 years…
Send your questions or comments to:
Toolsmartz@bellsouth.net and we’ll see what we can do to help you.
We lived in Memphis, TN and my dad was a truck driver. One Friday night in 1972, he came home and told my mom that they had to make a road trip the next day. He wouldn’t tell me why. They got up early on Saturday and late that afternoon, they came back, with my mom driving our ‘normal’ car and dad was driving…well...what was that? It turned out to be a 1950 Ford Crestliner that he found in Gordo, AL. His first words about it were- “You need to fix the brakes”.
The drivetrain had been replaced with 1964 Falcon Sprint components – a 260ci V8, a four speed trans and an 8 inch rear. The vinyl top had been sprayed on and the original Coronation Red metallic had some funky green painted over it…but it was MINE!
Over the next few months I learned to arc weld because I had to constantly change out the exhaust system. I’d go thru city inspection with a normal muffler and get home and swap it out for a Thrush glasspack.
The speedometer didn’t work, so there is no telling how many miles I racked up on that car over the next 6-7 years. I joined the Navy in ’73 and took the car to Virginia and back, several times. Then we transferred to Florida and drove it down there…breaking the rearend gear when we hit the state line.
We went thru 5 different paint jobs over the next 33 years, one engine overhaul, a fresh rearend and many, many gallons of gas. In 1980, I swapped in a 1965, 396ci Chevy motor with a powerglide. While the ‘Ford guy’ in me wanted to keep it all Ford, that 396 dropped in so sweetly that it would have been a crime not to put it in.
When I remarried in 2003, I still had my Crestliner- still in primer, didn’t run, no interior…a true ‘project car’. My new, lovely wife, decided she had seen enough of the primer and she wanted to go cruising, so we had the car done right by The Hot Rod Shop in Corinth, MS. The 50’s parts list reads like a who’s who of automotive goodies: 1965 Chevy 396, 700r4 trans, Fatman spindles, power windows, killer stereo system, front disc brakes, 2003 Mustang Laser Red and ’73 GMC Sliver paint, 2003 Chrysler Sebring convertible front seats and whitewall radials.
This is our cruiser and there is no telling where we might show up…not too bad for a 60 year old car that I have owned for 38 years…
Send your questions or comments to:
Toolsmartz@bellsouth.net and we’ll see what we can do to help you.
Friday, April 23, 2010
#13 - Yes, Martha, she is a movie star.
I think we’ll take a ‘detour’ this week and let you know more about my other passion - aside from the care and feeding of woodworking machines and Taylor-Tot strollers. I love Hot Rods - Ol’ Skool, fire-breathing Hot Rods.
I have a 1934 Ford 5-window coupe that my dad bought in MS in 1958. You might have seen us driving it around the area. It’s yellow and black with whitewall tires and a 1936 flathead motor. We’re members of the Stones River Region of The Antique Automobile Club of America and our clubhouse is the old car garage at Cannonsburgh. Come see us sometime when there is an event at Cannonsburgh. We’re usually there.
What brings this up is that we finally got to see the movie about Billy Graham’s early years and my little Hot Rod is in it. Back in the spring of 2008, I got a call from a fellow who supplies cars for movies in this area and he said they needed some early 30’s era cars for a tent revival scene that was being shot on the back acreage of the Wilson County Fairgrounds. So, I put the full hood on the car and drove up there. Back in the day, they used to line the cars up around those tents and use their headlights to light up the inside. So, the first thing we did was set up for the scene where everyone is headed into the tent. The camera was on a real high boom and looking down on the area. In the movie, you can see my Hot Rod on the right side of the tent, all the way back at the end, but she IS there.
The next scene we did involved a lot of shooting inside the tent, so they moved me to the back side of the tent. I think it was because I have changed my car over to 12volt and my headlights were brighter than the other cars. Anyway, we sat on the back side thru all of the ‘under the tent’ dialogue and if you look closely when they show those scenes, you can see the front end of our car over the actor’s shoulders. We’re the one with those incredibly bright lights.
It was a really interesting night, and yes, I do mean night because it took ALL night to get the shots they wanted. Let me tell you, I was one tired motor-scooter that next day. Sleeping in a small 1934 Ford with no heat will do that for ya.
Send your questions or comments to:
Toolsmartz@bellsouth.net and we’ll see what we can do to help you.
_______________________________________________________________
Any views or opinions presented in this article are solely those of the author and do not necessarily represent those of this newspaper. Neither the author, nor this newspaper, accepts any liability for the content of this article, or for the consequences of any actions taken on the basis of the information provided.
Writer's NOTE: there is a related blog post on April 21, 2008.
I have a 1934 Ford 5-window coupe that my dad bought in MS in 1958. You might have seen us driving it around the area. It’s yellow and black with whitewall tires and a 1936 flathead motor. We’re members of the Stones River Region of The Antique Automobile Club of America and our clubhouse is the old car garage at Cannonsburgh. Come see us sometime when there is an event at Cannonsburgh. We’re usually there.
What brings this up is that we finally got to see the movie about Billy Graham’s early years and my little Hot Rod is in it. Back in the spring of 2008, I got a call from a fellow who supplies cars for movies in this area and he said they needed some early 30’s era cars for a tent revival scene that was being shot on the back acreage of the Wilson County Fairgrounds. So, I put the full hood on the car and drove up there. Back in the day, they used to line the cars up around those tents and use their headlights to light up the inside. So, the first thing we did was set up for the scene where everyone is headed into the tent. The camera was on a real high boom and looking down on the area. In the movie, you can see my Hot Rod on the right side of the tent, all the way back at the end, but she IS there.
The next scene we did involved a lot of shooting inside the tent, so they moved me to the back side of the tent. I think it was because I have changed my car over to 12volt and my headlights were brighter than the other cars. Anyway, we sat on the back side thru all of the ‘under the tent’ dialogue and if you look closely when they show those scenes, you can see the front end of our car over the actor’s shoulders. We’re the one with those incredibly bright lights.
It was a really interesting night, and yes, I do mean night because it took ALL night to get the shots they wanted. Let me tell you, I was one tired motor-scooter that next day. Sleeping in a small 1934 Ford with no heat will do that for ya.
Send your questions or comments to:
Toolsmartz@bellsouth.net and we’ll see what we can do to help you.
_______________________________________________________________
Any views or opinions presented in this article are solely those of the author and do not necessarily represent those of this newspaper. Neither the author, nor this newspaper, accepts any liability for the content of this article, or for the consequences of any actions taken on the basis of the information provided.
Writer's NOTE: there is a related blog post on April 21, 2008.
Sunday, April 18, 2010
#12- Is there a ‘whole lotta shakin goin on’?
Not in California or Haiti – Although, that was the case recently when the Earth decided to move underneath them. I’m talking about wheel vibration in your stationary Bandsaw. Usually they are a 12”, 14”, or 16” size. For the purpose of this column, I’m talking about those Bandsaws that have a drive belt from the motor to the bottom wheel.
So, let’s say that you have one of those Bandsaws and you’ve always noticed that it seems to vibrate rather bad while you’re using it. You’ve taken the blade off and run it with just the bottom wheel in action and it still ‘shakes, rattles and rolls’. Or maybe you took the blade off and just running the bottom wheel shows that it runs as smooth as a Hunter ceiling fan. What to do?
First off, isolate the vibration – chase it down. If your saw is vibrating, take the blade off and run just the motor and the bottom wheel. If that smoothes it out, your problem is in the upper wheel. If you run the bottom wheel only and it still vibrates, the problem is in the bottom wheel or the drive system. Take the drive belt off and run just the motor. If it still vibrates with only the motor running, check the tightness of the motor pulley. If the pulley’s tight and yet it still has excessive vibration with only the motor running, I’d suspect you have a bad motor.
From this point, let’s say it smoothed out after you took the blade off. You’ve got the wheel guard open, so you can get to the top wheel. Give the wheel a good spin - enough so that it can rotate for at least 10 revolutions. When it finally stops, make a witness mark at the bottom of the wheel so that you can see it. Give it another good spin and let it stop again. Check where your witness mark is. If the mark is close to the same spot at the bottom, do the spin test again and see where the mark ends up. Do this 5 times and if the mark ends up stopping in the same area at the bottom of the wheel 3 times out of 5 tests, your top wheel is off-balance and needs to be replaced.
The test for bottom wheel balance is the same, but you will need to remove the drive belt before the test. The idea is to spin just the bottom wheel, not the motor and drive belt, too.
Send your questions or comments to:
Toolsmartz@bellsouth.net and we’ll see what we can do to help you.
_______________________________________________________________
Any views or opinions presented in this article are solely those of the author and do not necessarily represent those of this newspaper. Neither the author, nor this newspaper, accepts any liability for the content of this article, or for the consequences of any actions taken on the basis of the information provided.
So, let’s say that you have one of those Bandsaws and you’ve always noticed that it seems to vibrate rather bad while you’re using it. You’ve taken the blade off and run it with just the bottom wheel in action and it still ‘shakes, rattles and rolls’. Or maybe you took the blade off and just running the bottom wheel shows that it runs as smooth as a Hunter ceiling fan. What to do?
First off, isolate the vibration – chase it down. If your saw is vibrating, take the blade off and run just the motor and the bottom wheel. If that smoothes it out, your problem is in the upper wheel. If you run the bottom wheel only and it still vibrates, the problem is in the bottom wheel or the drive system. Take the drive belt off and run just the motor. If it still vibrates with only the motor running, check the tightness of the motor pulley. If the pulley’s tight and yet it still has excessive vibration with only the motor running, I’d suspect you have a bad motor.
From this point, let’s say it smoothed out after you took the blade off. You’ve got the wheel guard open, so you can get to the top wheel. Give the wheel a good spin - enough so that it can rotate for at least 10 revolutions. When it finally stops, make a witness mark at the bottom of the wheel so that you can see it. Give it another good spin and let it stop again. Check where your witness mark is. If the mark is close to the same spot at the bottom, do the spin test again and see where the mark ends up. Do this 5 times and if the mark ends up stopping in the same area at the bottom of the wheel 3 times out of 5 tests, your top wheel is off-balance and needs to be replaced.
The test for bottom wheel balance is the same, but you will need to remove the drive belt before the test. The idea is to spin just the bottom wheel, not the motor and drive belt, too.
Send your questions or comments to:
Toolsmartz@bellsouth.net and we’ll see what we can do to help you.
_______________________________________________________________
Any views or opinions presented in this article are solely those of the author and do not necessarily represent those of this newspaper. Neither the author, nor this newspaper, accepts any liability for the content of this article, or for the consequences of any actions taken on the basis of the information provided.
Friday, April 9, 2010
#11 - What about surface rusting on your tools?
We got a good question from Donald in Arlington, TN for this week (my, does our paper get around or what?). Donald says: “I don’t use my woodworking machines a lot, but when I do try to use them, they have a coat of rust on the tables. How do I stop that?” Hint: the more you use your tools, the less rust will be able to grow on them.
While I am tempted to just answer Donald’s question, I think you all might be better served by knowing what to do when you find the rust, then we can learn how to prevent it. First off is to clean the rust from the surface. How to do that really depends on how severe the rust is. For this column we’ll just deal with light surface rust. You can use fine or medium size steel wool, or a palm sander with 220 or 400 grit paper, or even wet or dry sandpaper and sand the rust off. My favorite method is to use a sanding block with 220 grit ‘wet or dry’ sandpaper and sprinkle a bit of nail polish remover (acetone) on the table and use that as the paper’s lubricant. Sand the whole table and then wipe the surface thoroughly with clean rags soaked in acetone. Once the surface is clean, dry the area very good…because now comes the ‘How do I stop that?’ part.
The ‘old school’ method is to coat a good rust-free surface with Johnsons paste floor wax and lightly buff it. Don’t remove all the wax, just try to make the coat spread evenly. The modern ‘hip’ method is to use a product called Boeshield T-9® (you can find it at Sears) and follow the directions on the package. CAUTION: Do NOT use automotive wax. Most of them have a high water content and will actually cause the rust you are trying to prevent.
On woodworking tool surfaces Boeshield T-9® recently topped all other surface treatments in Wood Magazine's article on “Rust Busters”.
The formulation is based on a unique combination of solvents and waxes and is designed to penetrate metal pores and dissolve minor corrosion, then leave a resilient waxy coating that lasts for many months.
During my years in Technical Service on woodworking machinery, we consistently recommended the paste floor wax and our customers had great success using it. It’s like a ‘tried and true’ method for preventing surface rust. Fortunately, I’ve heard so many good things about Boeshield T-9® that I am confident in it, also. Thanks for your question, Donald.
Send your questions or comments to:
Toolsmartz@bellsouth.net and we’ll see what we can do to help you.
_______________________________________________________________
Any views or opinions presented in this article are solely those of the author and do not necessarily represent those of this newspaper. Neither the author, nor this newspaper, accepts any liability for the content of this article, or for the consequences of any actions taken on the basis of the information provided.
While I am tempted to just answer Donald’s question, I think you all might be better served by knowing what to do when you find the rust, then we can learn how to prevent it. First off is to clean the rust from the surface. How to do that really depends on how severe the rust is. For this column we’ll just deal with light surface rust. You can use fine or medium size steel wool, or a palm sander with 220 or 400 grit paper, or even wet or dry sandpaper and sand the rust off. My favorite method is to use a sanding block with 220 grit ‘wet or dry’ sandpaper and sprinkle a bit of nail polish remover (acetone) on the table and use that as the paper’s lubricant. Sand the whole table and then wipe the surface thoroughly with clean rags soaked in acetone. Once the surface is clean, dry the area very good…because now comes the ‘How do I stop that?’ part.
The ‘old school’ method is to coat a good rust-free surface with Johnsons paste floor wax and lightly buff it. Don’t remove all the wax, just try to make the coat spread evenly. The modern ‘hip’ method is to use a product called Boeshield T-9® (you can find it at Sears) and follow the directions on the package. CAUTION: Do NOT use automotive wax. Most of them have a high water content and will actually cause the rust you are trying to prevent.
On woodworking tool surfaces Boeshield T-9® recently topped all other surface treatments in Wood Magazine's article on “Rust Busters”.
The formulation is based on a unique combination of solvents and waxes and is designed to penetrate metal pores and dissolve minor corrosion, then leave a resilient waxy coating that lasts for many months.
During my years in Technical Service on woodworking machinery, we consistently recommended the paste floor wax and our customers had great success using it. It’s like a ‘tried and true’ method for preventing surface rust. Fortunately, I’ve heard so many good things about Boeshield T-9® that I am confident in it, also. Thanks for your question, Donald.
Send your questions or comments to:
Toolsmartz@bellsouth.net and we’ll see what we can do to help you.
_______________________________________________________________
Any views or opinions presented in this article are solely those of the author and do not necessarily represent those of this newspaper. Neither the author, nor this newspaper, accepts any liability for the content of this article, or for the consequences of any actions taken on the basis of the information provided.
Friday, April 2, 2010
Love them little young'uns...and their parents, too!
We had a really good weekend last weekend. My daughter and her family came over from Arlington to visit with us for a few days and it was a real hoot.
I had wondered how the interaction between the kids and our rescued Cocker Spaniel would go and I don't think it could have gone much better at all. Once the kids got past the idea that Winston was going to bite their faces off, they had a good time. Wintston was a trooper - he heard 'squeaky' (his toy) squeaked more times that he had ever heard and had to really listen close to obey the kids when they told him to sit or play dead or speak... but the kids were amazed that he obeyed them. Actually, I was too - I had no idea how he would act...but he IS a good dog.
We had a couple of treasured moments that I just HAD to put on here...
First is a picture of all of our 'pets' in their "on your back" pose..
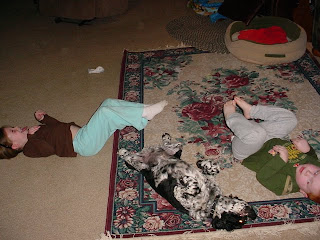
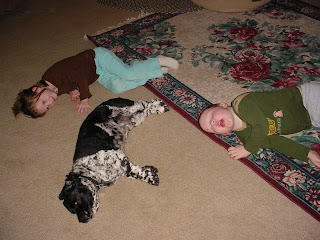
It really was a sight with Evan running thru the house with Winston right behind...or Ella sitting within reach and getting a fresh 'kiss' from Winston.
I think they all had fun and we did too.
I had wondered how the interaction between the kids and our rescued Cocker Spaniel would go and I don't think it could have gone much better at all. Once the kids got past the idea that Winston was going to bite their faces off, they had a good time. Wintston was a trooper - he heard 'squeaky' (his toy) squeaked more times that he had ever heard and had to really listen close to obey the kids when they told him to sit or play dead or speak... but the kids were amazed that he obeyed them. Actually, I was too - I had no idea how he would act...but he IS a good dog.
We had a couple of treasured moments that I just HAD to put on here...
First is a picture of all of our 'pets' in their "on your back" pose..
And then we had them all playing "Dead Dog".
It really was a sight with Evan running thru the house with Winston right behind...or Ella sitting within reach and getting a fresh 'kiss' from Winston.
I think they all had fun and we did too.
# 10- Static Electricity in your Woodshop
This week let’s talk about static electricity in your woodshop. I’m sure we’ve all experienced it when using our belt sanders, but it can show up on all rotating equipment and especially in your dust collector ducts.
Static electricity in a wood shop is mainly caused by two things. First is low humidity in the air. Static is especially troublesome in winter when the outside temperatures are low. A rule of thumb is the colder it is outside, the lower the humidity is inside a heated shop. As a result, static charge builds up easily and causes shocks when the electricity discharges through contact. The problem is even worse if a shop’s dust collection system exhausts its air outside the building. This builds an additional requirement for fresh air coming in and the fresh, cold air will have low humidity once it has been heated indoors.
The second thing that causes the static electricity problem is motion between two things. In the case of a belt sander, it is the motion between the belt, platen and pulleys that causes the build-up of electricity. In the case of the dust collector or Shop-Vac, it is the motion of the particles through the hose. There are two places where the charge can build up. One is in the machine the dust collector is attached to and the other is on the person who is operating it. Fortunately, grounding the frame of the machine will eliminate the buildup of the static charge. All fixed machinery, such as a table saw, jointer, planer etc., should have its frame grounded to a water pipe or at the very least, to the ground conductor or conduit sheath of the machine’s electrical wiring. Sometimes this is not possible, especially if the machine is electrically double insulated, as is the Shop-Vac.
Beyond grounding the machine, the best cure for static problems is to try to keep the humidity in the shop from getting too low. This can be done by using bag-type dust collectors that re-circulate the same air within the shop after the dust has been removed. These collectors will also reduce your heating bill. Other ways of adding moisture to the air, such as using humidifiers, are worth considering. Another thing you can do is wear shoes that bleed off the static charge rather than allowing it to build up.
Send your questions or comments to:
Toolsmartz@bellsouth.net and we’ll see what we can do to help you.
_______________________________________________________________
Any views or opinions presented in this article are solely those of the author and do not necessarily represent those of this newspaper. Neither the author, nor this newspaper, accepts any liability for the content of this article, or for the consequences of any actions taken on the basis of the information provided.
Static electricity in a wood shop is mainly caused by two things. First is low humidity in the air. Static is especially troublesome in winter when the outside temperatures are low. A rule of thumb is the colder it is outside, the lower the humidity is inside a heated shop. As a result, static charge builds up easily and causes shocks when the electricity discharges through contact. The problem is even worse if a shop’s dust collection system exhausts its air outside the building. This builds an additional requirement for fresh air coming in and the fresh, cold air will have low humidity once it has been heated indoors.
The second thing that causes the static electricity problem is motion between two things. In the case of a belt sander, it is the motion between the belt, platen and pulleys that causes the build-up of electricity. In the case of the dust collector or Shop-Vac, it is the motion of the particles through the hose. There are two places where the charge can build up. One is in the machine the dust collector is attached to and the other is on the person who is operating it. Fortunately, grounding the frame of the machine will eliminate the buildup of the static charge. All fixed machinery, such as a table saw, jointer, planer etc., should have its frame grounded to a water pipe or at the very least, to the ground conductor or conduit sheath of the machine’s electrical wiring. Sometimes this is not possible, especially if the machine is electrically double insulated, as is the Shop-Vac.
Beyond grounding the machine, the best cure for static problems is to try to keep the humidity in the shop from getting too low. This can be done by using bag-type dust collectors that re-circulate the same air within the shop after the dust has been removed. These collectors will also reduce your heating bill. Other ways of adding moisture to the air, such as using humidifiers, are worth considering. Another thing you can do is wear shoes that bleed off the static charge rather than allowing it to build up.
Send your questions or comments to:
Toolsmartz@bellsouth.net and we’ll see what we can do to help you.
_______________________________________________________________
Any views or opinions presented in this article are solely those of the author and do not necessarily represent those of this newspaper. Neither the author, nor this newspaper, accepts any liability for the content of this article, or for the consequences of any actions taken on the basis of the information provided.
Subscribe to:
Posts (Atom)