I think we’ll take a ‘detour’ this week and let you know more about my other passion - aside from the care and feeding of woodworking machines and Taylor-Tot strollers. I love Hot Rods - Ol’ Skool, fire-breathing Hot Rods.
I have a 1934 Ford 5-window coupe that my dad bought in MS in 1958. You might have seen us driving it around the area. It’s yellow and black with whitewall tires and a 1936 flathead motor. We’re members of the Stones River Region of The Antique Automobile Club of America and our clubhouse is the old car garage at Cannonsburgh. Come see us sometime when there is an event at Cannonsburgh. We’re usually there.
What brings this up is that we finally got to see the movie about Billy Graham’s early years and my little Hot Rod is in it. Back in the spring of 2008, I got a call from a fellow who supplies cars for movies in this area and he said they needed some early 30’s era cars for a tent revival scene that was being shot on the back acreage of the Wilson County Fairgrounds. So, I put the full hood on the car and drove up there. Back in the day, they used to line the cars up around those tents and use their headlights to light up the inside. So, the first thing we did was set up for the scene where everyone is headed into the tent. The camera was on a real high boom and looking down on the area. In the movie, you can see my Hot Rod on the right side of the tent, all the way back at the end, but she IS there.
The next scene we did involved a lot of shooting inside the tent, so they moved me to the back side of the tent. I think it was because I have changed my car over to 12volt and my headlights were brighter than the other cars. Anyway, we sat on the back side thru all of the ‘under the tent’ dialogue and if you look closely when they show those scenes, you can see the front end of our car over the actor’s shoulders. We’re the one with those incredibly bright lights.
It was a really interesting night, and yes, I do mean night because it took ALL night to get the shots they wanted. Let me tell you, I was one tired motor-scooter that next day. Sleeping in a small 1934 Ford with no heat will do that for ya.
Send your questions or comments to:
Toolsmartz@bellsouth.net and we’ll see what we can do to help you.
_______________________________________________________________
Any views or opinions presented in this article are solely those of the author and do not necessarily represent those of this newspaper. Neither the author, nor this newspaper, accepts any liability for the content of this article, or for the consequences of any actions taken on the basis of the information provided.
Writer's NOTE: there is a related blog post on April 21, 2008.
Friday, April 23, 2010
Sunday, April 18, 2010
#12- Is there a ‘whole lotta shakin goin on’?
Not in California or Haiti – Although, that was the case recently when the Earth decided to move underneath them. I’m talking about wheel vibration in your stationary Bandsaw. Usually they are a 12”, 14”, or 16” size. For the purpose of this column, I’m talking about those Bandsaws that have a drive belt from the motor to the bottom wheel.
So, let’s say that you have one of those Bandsaws and you’ve always noticed that it seems to vibrate rather bad while you’re using it. You’ve taken the blade off and run it with just the bottom wheel in action and it still ‘shakes, rattles and rolls’. Or maybe you took the blade off and just running the bottom wheel shows that it runs as smooth as a Hunter ceiling fan. What to do?
First off, isolate the vibration – chase it down. If your saw is vibrating, take the blade off and run just the motor and the bottom wheel. If that smoothes it out, your problem is in the upper wheel. If you run the bottom wheel only and it still vibrates, the problem is in the bottom wheel or the drive system. Take the drive belt off and run just the motor. If it still vibrates with only the motor running, check the tightness of the motor pulley. If the pulley’s tight and yet it still has excessive vibration with only the motor running, I’d suspect you have a bad motor.
From this point, let’s say it smoothed out after you took the blade off. You’ve got the wheel guard open, so you can get to the top wheel. Give the wheel a good spin - enough so that it can rotate for at least 10 revolutions. When it finally stops, make a witness mark at the bottom of the wheel so that you can see it. Give it another good spin and let it stop again. Check where your witness mark is. If the mark is close to the same spot at the bottom, do the spin test again and see where the mark ends up. Do this 5 times and if the mark ends up stopping in the same area at the bottom of the wheel 3 times out of 5 tests, your top wheel is off-balance and needs to be replaced.
The test for bottom wheel balance is the same, but you will need to remove the drive belt before the test. The idea is to spin just the bottom wheel, not the motor and drive belt, too.
Send your questions or comments to:
Toolsmartz@bellsouth.net and we’ll see what we can do to help you.
_______________________________________________________________
Any views or opinions presented in this article are solely those of the author and do not necessarily represent those of this newspaper. Neither the author, nor this newspaper, accepts any liability for the content of this article, or for the consequences of any actions taken on the basis of the information provided.
So, let’s say that you have one of those Bandsaws and you’ve always noticed that it seems to vibrate rather bad while you’re using it. You’ve taken the blade off and run it with just the bottom wheel in action and it still ‘shakes, rattles and rolls’. Or maybe you took the blade off and just running the bottom wheel shows that it runs as smooth as a Hunter ceiling fan. What to do?
First off, isolate the vibration – chase it down. If your saw is vibrating, take the blade off and run just the motor and the bottom wheel. If that smoothes it out, your problem is in the upper wheel. If you run the bottom wheel only and it still vibrates, the problem is in the bottom wheel or the drive system. Take the drive belt off and run just the motor. If it still vibrates with only the motor running, check the tightness of the motor pulley. If the pulley’s tight and yet it still has excessive vibration with only the motor running, I’d suspect you have a bad motor.
From this point, let’s say it smoothed out after you took the blade off. You’ve got the wheel guard open, so you can get to the top wheel. Give the wheel a good spin - enough so that it can rotate for at least 10 revolutions. When it finally stops, make a witness mark at the bottom of the wheel so that you can see it. Give it another good spin and let it stop again. Check where your witness mark is. If the mark is close to the same spot at the bottom, do the spin test again and see where the mark ends up. Do this 5 times and if the mark ends up stopping in the same area at the bottom of the wheel 3 times out of 5 tests, your top wheel is off-balance and needs to be replaced.
The test for bottom wheel balance is the same, but you will need to remove the drive belt before the test. The idea is to spin just the bottom wheel, not the motor and drive belt, too.
Send your questions or comments to:
Toolsmartz@bellsouth.net and we’ll see what we can do to help you.
_______________________________________________________________
Any views or opinions presented in this article are solely those of the author and do not necessarily represent those of this newspaper. Neither the author, nor this newspaper, accepts any liability for the content of this article, or for the consequences of any actions taken on the basis of the information provided.
Friday, April 9, 2010
#11 - What about surface rusting on your tools?
We got a good question from Donald in Arlington, TN for this week (my, does our paper get around or what?). Donald says: “I don’t use my woodworking machines a lot, but when I do try to use them, they have a coat of rust on the tables. How do I stop that?” Hint: the more you use your tools, the less rust will be able to grow on them.
While I am tempted to just answer Donald’s question, I think you all might be better served by knowing what to do when you find the rust, then we can learn how to prevent it. First off is to clean the rust from the surface. How to do that really depends on how severe the rust is. For this column we’ll just deal with light surface rust. You can use fine or medium size steel wool, or a palm sander with 220 or 400 grit paper, or even wet or dry sandpaper and sand the rust off. My favorite method is to use a sanding block with 220 grit ‘wet or dry’ sandpaper and sprinkle a bit of nail polish remover (acetone) on the table and use that as the paper’s lubricant. Sand the whole table and then wipe the surface thoroughly with clean rags soaked in acetone. Once the surface is clean, dry the area very good…because now comes the ‘How do I stop that?’ part.
The ‘old school’ method is to coat a good rust-free surface with Johnsons paste floor wax and lightly buff it. Don’t remove all the wax, just try to make the coat spread evenly. The modern ‘hip’ method is to use a product called Boeshield T-9® (you can find it at Sears) and follow the directions on the package. CAUTION: Do NOT use automotive wax. Most of them have a high water content and will actually cause the rust you are trying to prevent.
On woodworking tool surfaces Boeshield T-9® recently topped all other surface treatments in Wood Magazine's article on “Rust Busters”.
The formulation is based on a unique combination of solvents and waxes and is designed to penetrate metal pores and dissolve minor corrosion, then leave a resilient waxy coating that lasts for many months.
During my years in Technical Service on woodworking machinery, we consistently recommended the paste floor wax and our customers had great success using it. It’s like a ‘tried and true’ method for preventing surface rust. Fortunately, I’ve heard so many good things about Boeshield T-9® that I am confident in it, also. Thanks for your question, Donald.
Send your questions or comments to:
Toolsmartz@bellsouth.net and we’ll see what we can do to help you.
_______________________________________________________________
Any views or opinions presented in this article are solely those of the author and do not necessarily represent those of this newspaper. Neither the author, nor this newspaper, accepts any liability for the content of this article, or for the consequences of any actions taken on the basis of the information provided.
While I am tempted to just answer Donald’s question, I think you all might be better served by knowing what to do when you find the rust, then we can learn how to prevent it. First off is to clean the rust from the surface. How to do that really depends on how severe the rust is. For this column we’ll just deal with light surface rust. You can use fine or medium size steel wool, or a palm sander with 220 or 400 grit paper, or even wet or dry sandpaper and sand the rust off. My favorite method is to use a sanding block with 220 grit ‘wet or dry’ sandpaper and sprinkle a bit of nail polish remover (acetone) on the table and use that as the paper’s lubricant. Sand the whole table and then wipe the surface thoroughly with clean rags soaked in acetone. Once the surface is clean, dry the area very good…because now comes the ‘How do I stop that?’ part.
The ‘old school’ method is to coat a good rust-free surface with Johnsons paste floor wax and lightly buff it. Don’t remove all the wax, just try to make the coat spread evenly. The modern ‘hip’ method is to use a product called Boeshield T-9® (you can find it at Sears) and follow the directions on the package. CAUTION: Do NOT use automotive wax. Most of them have a high water content and will actually cause the rust you are trying to prevent.
On woodworking tool surfaces Boeshield T-9® recently topped all other surface treatments in Wood Magazine's article on “Rust Busters”.
The formulation is based on a unique combination of solvents and waxes and is designed to penetrate metal pores and dissolve minor corrosion, then leave a resilient waxy coating that lasts for many months.
During my years in Technical Service on woodworking machinery, we consistently recommended the paste floor wax and our customers had great success using it. It’s like a ‘tried and true’ method for preventing surface rust. Fortunately, I’ve heard so many good things about Boeshield T-9® that I am confident in it, also. Thanks for your question, Donald.
Send your questions or comments to:
Toolsmartz@bellsouth.net and we’ll see what we can do to help you.
_______________________________________________________________
Any views or opinions presented in this article are solely those of the author and do not necessarily represent those of this newspaper. Neither the author, nor this newspaper, accepts any liability for the content of this article, or for the consequences of any actions taken on the basis of the information provided.
Friday, April 2, 2010
Love them little young'uns...and their parents, too!
We had a really good weekend last weekend. My daughter and her family came over from Arlington to visit with us for a few days and it was a real hoot.
I had wondered how the interaction between the kids and our rescued Cocker Spaniel would go and I don't think it could have gone much better at all. Once the kids got past the idea that Winston was going to bite their faces off, they had a good time. Wintston was a trooper - he heard 'squeaky' (his toy) squeaked more times that he had ever heard and had to really listen close to obey the kids when they told him to sit or play dead or speak... but the kids were amazed that he obeyed them. Actually, I was too - I had no idea how he would act...but he IS a good dog.
We had a couple of treasured moments that I just HAD to put on here...
First is a picture of all of our 'pets' in their "on your back" pose..
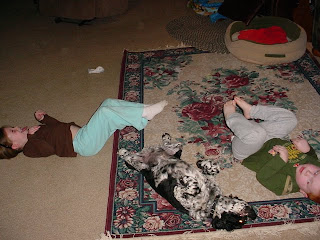
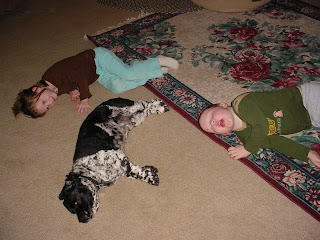
It really was a sight with Evan running thru the house with Winston right behind...or Ella sitting within reach and getting a fresh 'kiss' from Winston.
I think they all had fun and we did too.
I had wondered how the interaction between the kids and our rescued Cocker Spaniel would go and I don't think it could have gone much better at all. Once the kids got past the idea that Winston was going to bite their faces off, they had a good time. Wintston was a trooper - he heard 'squeaky' (his toy) squeaked more times that he had ever heard and had to really listen close to obey the kids when they told him to sit or play dead or speak... but the kids were amazed that he obeyed them. Actually, I was too - I had no idea how he would act...but he IS a good dog.
We had a couple of treasured moments that I just HAD to put on here...
First is a picture of all of our 'pets' in their "on your back" pose..
And then we had them all playing "Dead Dog".
It really was a sight with Evan running thru the house with Winston right behind...or Ella sitting within reach and getting a fresh 'kiss' from Winston.
I think they all had fun and we did too.
# 10- Static Electricity in your Woodshop
This week let’s talk about static electricity in your woodshop. I’m sure we’ve all experienced it when using our belt sanders, but it can show up on all rotating equipment and especially in your dust collector ducts.
Static electricity in a wood shop is mainly caused by two things. First is low humidity in the air. Static is especially troublesome in winter when the outside temperatures are low. A rule of thumb is the colder it is outside, the lower the humidity is inside a heated shop. As a result, static charge builds up easily and causes shocks when the electricity discharges through contact. The problem is even worse if a shop’s dust collection system exhausts its air outside the building. This builds an additional requirement for fresh air coming in and the fresh, cold air will have low humidity once it has been heated indoors.
The second thing that causes the static electricity problem is motion between two things. In the case of a belt sander, it is the motion between the belt, platen and pulleys that causes the build-up of electricity. In the case of the dust collector or Shop-Vac, it is the motion of the particles through the hose. There are two places where the charge can build up. One is in the machine the dust collector is attached to and the other is on the person who is operating it. Fortunately, grounding the frame of the machine will eliminate the buildup of the static charge. All fixed machinery, such as a table saw, jointer, planer etc., should have its frame grounded to a water pipe or at the very least, to the ground conductor or conduit sheath of the machine’s electrical wiring. Sometimes this is not possible, especially if the machine is electrically double insulated, as is the Shop-Vac.
Beyond grounding the machine, the best cure for static problems is to try to keep the humidity in the shop from getting too low. This can be done by using bag-type dust collectors that re-circulate the same air within the shop after the dust has been removed. These collectors will also reduce your heating bill. Other ways of adding moisture to the air, such as using humidifiers, are worth considering. Another thing you can do is wear shoes that bleed off the static charge rather than allowing it to build up.
Send your questions or comments to:
Toolsmartz@bellsouth.net and we’ll see what we can do to help you.
_______________________________________________________________
Any views or opinions presented in this article are solely those of the author and do not necessarily represent those of this newspaper. Neither the author, nor this newspaper, accepts any liability for the content of this article, or for the consequences of any actions taken on the basis of the information provided.
Static electricity in a wood shop is mainly caused by two things. First is low humidity in the air. Static is especially troublesome in winter when the outside temperatures are low. A rule of thumb is the colder it is outside, the lower the humidity is inside a heated shop. As a result, static charge builds up easily and causes shocks when the electricity discharges through contact. The problem is even worse if a shop’s dust collection system exhausts its air outside the building. This builds an additional requirement for fresh air coming in and the fresh, cold air will have low humidity once it has been heated indoors.
The second thing that causes the static electricity problem is motion between two things. In the case of a belt sander, it is the motion between the belt, platen and pulleys that causes the build-up of electricity. In the case of the dust collector or Shop-Vac, it is the motion of the particles through the hose. There are two places where the charge can build up. One is in the machine the dust collector is attached to and the other is on the person who is operating it. Fortunately, grounding the frame of the machine will eliminate the buildup of the static charge. All fixed machinery, such as a table saw, jointer, planer etc., should have its frame grounded to a water pipe or at the very least, to the ground conductor or conduit sheath of the machine’s electrical wiring. Sometimes this is not possible, especially if the machine is electrically double insulated, as is the Shop-Vac.
Beyond grounding the machine, the best cure for static problems is to try to keep the humidity in the shop from getting too low. This can be done by using bag-type dust collectors that re-circulate the same air within the shop after the dust has been removed. These collectors will also reduce your heating bill. Other ways of adding moisture to the air, such as using humidifiers, are worth considering. Another thing you can do is wear shoes that bleed off the static charge rather than allowing it to build up.
Send your questions or comments to:
Toolsmartz@bellsouth.net and we’ll see what we can do to help you.
_______________________________________________________________
Any views or opinions presented in this article are solely those of the author and do not necessarily represent those of this newspaper. Neither the author, nor this newspaper, accepts any liability for the content of this article, or for the consequences of any actions taken on the basis of the information provided.
Subscribe to:
Posts (Atom)